How Cross-Docking Can Improve Efficiency and Reduce Costs in Warehousing
15 min read
60-Second Summary
Many businesses today face growing pressure to deliver products faster while cutting costs. Cross-docking is a powerful warehouse strategy that helps achieve both by reducing storage time and streamlining how products move from incoming shipments to outbound carriers. Instead of sitting in storage, goods are quickly sorted and shipped—ideal for perishable, time-sensitive, or bulk items. This approach not only accelerates delivery speeds, meeting the high expectations of online shoppers, but also cuts expenses, increases inventory turnover, and improves customer satisfaction. With nearly two-thirds of consumers wanting purchases in under 24 hours, cross-docking gives warehouses the agility to meet demand and maintain a competitive edge.
Many businesses are pressured to ship products much faster and more effectively as they balance meeting growing customer demands and cutting operational expenses. Cross-docking is an effective supply chain management strategy that can help you achieve these objectives, giving your warehouse a competitive advantage.
Understanding Cross-Docking Operations
Cross-docking accelerates the transfer of items from inbound shipments to outbound carriers. In contrast to traditional warehousing methods, which typically require extended inventory holding, cross-docking operations reduce handling and storage times by streamlining the flow of products in the supply chain. Once products arrive at a facility or warehouse, they are sorted before being shipped.
With items spending less time in storage, companies can fulfill orders much more efficiently, as they avoid delays caused by time-consuming processes such as locating items in a warehouse or complex picking workflows. Coss-docking can significantly speed up delivery times, making it ideal for shipping the following:
- Perishable items such as food or agricultural goods.
- Seasonal merchandise with a time-sensitive demand must be rapidly dispatched to stores.
- Bulk products with a steady demand.
- Items that don’t need inspection.
- Products that require temperature-controlled environments, such as medication.
With 46% of online shoppers wanting faster delivery, e-commerce retailers are also using cross-docking to meet these expectations and gain a competitive edge.
How Cross-Docking Improves Warehouse Operations
Cross-docking can improve your operations in many ways. Beyond allowing for expedited shipping, minimizing storage time can reduce various costs, increase inventory turnover, and enhance overall operational efficiency and customer satisfaction.
Increased Customer Satisfaction
Almost two-thirds of consumers worldwide want to receive their purchases in less than 24 hours, with four out of 10 shoppers expecting delivery in under two hours. Because cross-docking speeds up shipping, orders are more likely to arrive on time, which can increase customer satisfaction and retention rates.
Shoppers also expect businesses to have stock of the products they seek. Out-of-stock items may frustrate customers, causing them to take their business elsewhere. Cross-docking can help your operation become more flexible and agile as it allows for just-in-time (JIT) inventory management — a strategy in which you receive the exact amount of inventory required when you need it. As a result, you can be better equipped to respond quickly to shifts in market demand and conditions, replenishing your inventory according to customers’ needs and wants.
Higher Inventory Turnover Rates
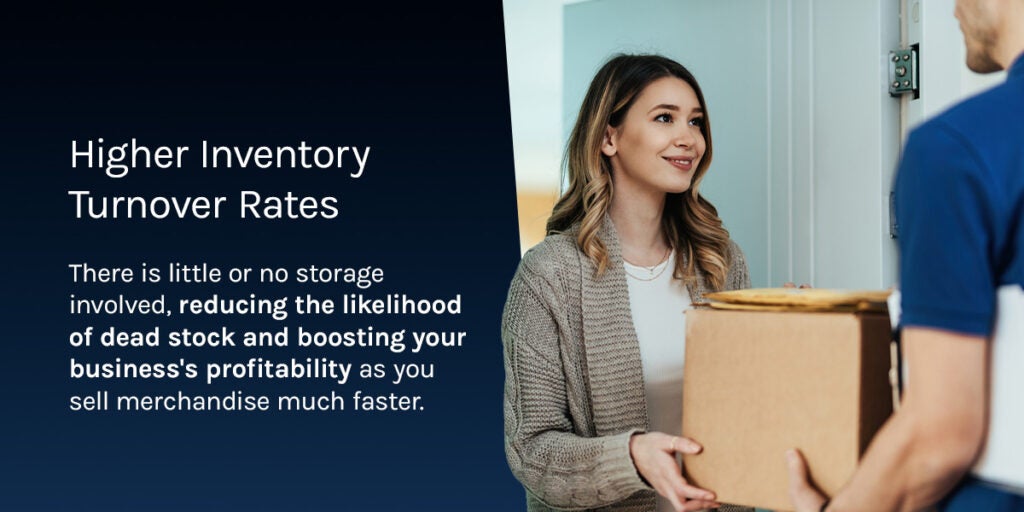
With cross-docking, goods move through the supply chain more rapidly. This typically leads to higher inventory turnover rates. There is little or no storage involved, reducing the likelihood of dead stock and boosting your business’s profitability as you sell merchandise much faster. JIT inventory management is also a cross-docking technique for increasing inventory turnover since it can help avoid excess stock.
Reduced Costs
You can achieve cost savings through cross-docking in the following ways:
- Storage and warehousing: As the need to store goods for prolonged periods is minimized or eliminated, you can save on storage-related expenses such as rent or tracking items in storage.
- Material handling: Less handling is necessary since items don’t need to be picked, put away in storage, and retrieved for shipping. Your employees only need to move products from inbound vehicles to outbound carriers, lowering labor costs with a more streamlined process.
- Transportation: Shipping is typically a significant cost for most businesses. Cross-docking can reduce these expenses by optimizing transfer transport routes and allowing direct transfer from incoming to outgoing vehicles.
Fewer Product-Related Risks
In most cases, the longer items are stored and the more they are handled, the higher the risk of damage. For example, workers can drop or stack products incorrectly, and perishable goods may expire. Because cross-docking cuts down on storage and handling, inventory loss, damaged products, and employee errors don’t occur as often. Shipping times are also accelerated, so products will likely be delivered in good condition, leading to happier customers and fewer returns.
Overcoming Challenges in Cross-Docking Operations with OPEX®
While warehouse cross-docking skips several steps involved in traditional order fulfillment, goods still need to be received and sorted before being transferred to outbound vehicles. Manual sortation can be a time-consuming and labor-dependent process, prone to delays and human errors. Even though you may have drastically cut down on costs by implementing cross-docking, labor expenditures make up 60%-65% of overall fulfillment expenses.
With automated sorting systems such as Sure Sort® and Sure Sort® X, you can ship pallets or cases of inventory and break them down into smaller units that are automatically sorted according to your various distribution centers or store locations. These systems use sensors, scanners, conveyors, and robotics to achieve rapid and error-free sortation. Partnering with OPEX® can help you overcome these challenges:
- Delayed processing times: Due to fluctuations in demand and the limited speed achieved by manual labor, congestion in processing often happens as items build up at specific points in the workflow. Sure Sort and Sure Sort X optimize the receiving, scanning, and sorting of items. With these technologies, items are placed onto conveyors and entered into the system, going through a six-sided scanning tunnel that can read RFID tags and up to eight barcodes. Next, iBot® systems or vehicles transport the goods to their allocated sorting location according to predetermined criteria. The iBots then deliver items to sort bins, ready for outgoing shipments.
- Labor shortages: Cross-docking often demands a sizable workforce to perform the scanning, sorting, and moving. As iBots automatically sort items, Sure Sort and Sure Sort X can minimize physical stress for your employees and reduce the amount of labor needed. With worldwide staffing shortages affecting many businesses, automation can make your operation more resilient by lessening its dependence on a human workforce.
- Space limitations: If your warehouse or facility has limited space, Sure Sort and Sure Sort X are ideal. With their compact design and clever use of space, these systems can replace as many as six manual put walls while offering a reduced physical footprint. All items are sorted into one consolidated location regardless of product size or type.
- Supply chain disruptions: Sure Sort and Sure Sort X can help you lessen the effects of supply chain disruptions by boosting the agility and flexibility that cross-docking offers. Both systems can handle sizable shipments, conveniently breaking these down into smaller categories for seamless delivery.
- High error rates: Manual sorting processes are more prone to mistakes, such as misplaced items or delays, which can negatively impact customer satisfaction. With Sure Sort and Sure Sort X’s cutting-edge scanning and sorting capabilities, you can create a more reliable, error-free operation.
Automate Sortation to Enhance Cross-Docking Efficiency
With nearly 50 years of experience and deep industry knowledge, OPEX is an industry leader in warehouse automation. We engineer and manufacture next-generation automation solutions, such as Sure Sort and Sure Sort X, which have won awards for their innovative capabilities.
Beyond accessing advanced sortation systems that can drastically enhance the efficiency of your cross-docking operations, you’ll receive 24/7 support from highly qualified technicians when you partner with OPEX. To begin automating your sorting processes, contact us today.
Other Resources You Might Find Helpful
Connecting Employees and Their Mail No Matter Where They Are
Georgia Department of Revenue Accelerates Processing Times By Automating The Open, Prep, And Scan Process
San Bernadino County Falcon+ Video
Swiss Post Solutions Delivers Innovation and Automation to Clients Leveraging The OPEX Falcon+® RED™
Claims Processing System No Longer Feels Like a Painful Root Canal
Medical Record Scanning Demonstration with the OPEX Falcon+ Scanner
Enhancing the Digitization Process at Iron Mountain Government Solutions
SPS and OPEX® Falcon+® RED® Document Scanners Provide Digitization at Sanitas
Improving Payment Processing at Image Remit® a Division of Cash Management Solutions®
Taking the Right Steps to Digital Mailroom Success
NEXT LEVEL AUTOMATION
Unlock Operational Efficiency with OPEX
OPEX is powering the future of automation. Contact us to learn more about how our vertically integrated automated solutions can help take your business to new heights.