Managing Labor Shortages with Technology: Balancing Automation and Workforce Optimization
8 min read
60-Second Summary
The warehousing industry faces significant labor shortages driven by high turnover rates and rising e-commerce demands. Automation technologies address these challenges by handling repetitive tasks, improving productivity, enhancing workplace safety, and reducing physical strain. Instead of replacing human talent, automation allows workers to focus on complex, higher-value activities. Strategic implementation, including employee training and phased integration, ensures long-term operational efficiency, workforce satisfaction, and sustainable growth in increasingly competitive markets.
The Labor Shortage Reality
The warehousing and logistics sectors have experienced continue to experience acute severe staffing challenges recently. With rising e-commerce demands, seasonal fluctuations, and changing workforce demographics, companies struggle to attract and retain the talent needed to maintain operations. According to industry data, warehouse positions have become increasingly difficult to fill, with turnover rates often exceeding 40% annually.
These shortages translate into significant operational hurdles:
- Difficulty meeting throughput and fulfillment targets
- Rising labor costs and overtime expenses
- Decreased accuracy and quality control
- Employee burnout and safety concerns
- Challenges in scaling operations during peak periods
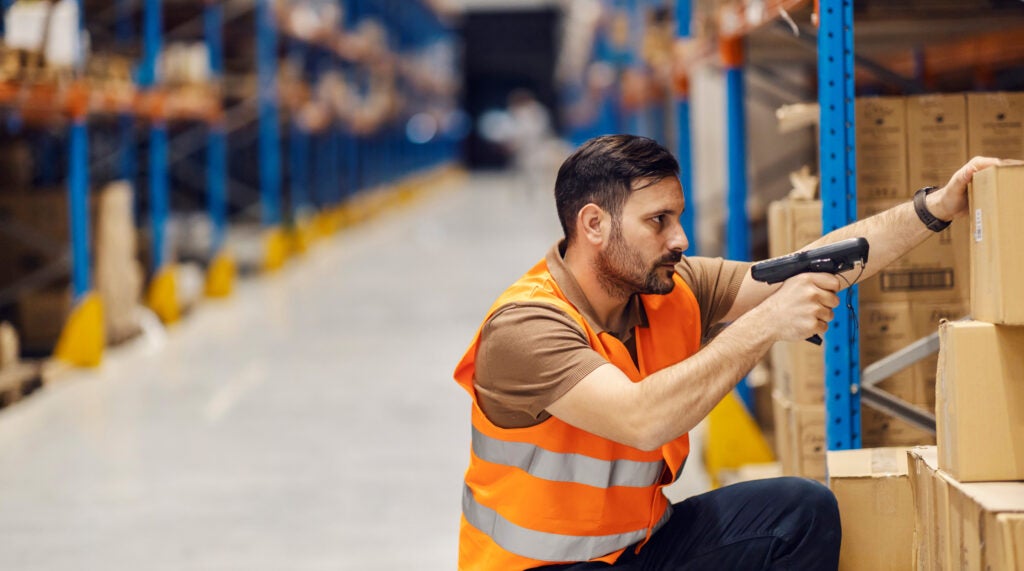
Automation As An Enabler, Not A Replacer
The solution isn’t simply replacing humans with machines. Rather, it’s about creating a strategic balance where technology handles repetitive, physically demanding tasks while human workers focus on higher-value activities that require creativity, problem-solving, and critical thinking. Two technologies, Automated Storage and Retrieval Systems (ASRS) automated storage and automated sorting systems, have emerged as game-changers effective solutions in addressing labor shortages while enhancing workforce productivity.Understanding ASRS and Automated Sorting Systems
Automated Storage and Retrieval Systems (ASRS)
AS/RS technology automates storing and retrieving warehouse goods, using robotic systems to place and pick inventory with minimal human intervention. These systems range from shuttle-based solutions and vertical lift modules (VLMs) to robotic retrieval and goods-to-person systems.Automated Sorting Systems
These technologies handle classifying, separating, and directing items, packages, and orders – tasks that traditionally require significant manual labor. These systems can process thousands of items hourly with remarkable precision using conveyor systems, sorters, robotics, and sophisticated control software.How Automation Address Labor Shortages
1. Reducing Labor Dependence While Improving Productivity
AS/RS and automated sorting systems directly impact labor requirements by handling repetitive, time-consuming tasks. A modern AS/RS can reduce manual labor needs by up to two-thirds while maintaining or increasing throughput rates. These systems operate continuously without breaks, fatigue, or absenteeism, ensuring predictable productivity even during labor shortages.Real World Success Stories
Rocky Mountain ATV: 45% Labor Reduction with Automated Sorting
Rocky Mountain ATV, a provider of OEM parts for dirt bikes, ATVs, and street bikes, faced significant challenges with its manual order fulfillment process. Before automation, its Kentucky distribution center required 20-25 employees who would walk 8-10 miles per shift to pick and sort parts by hand.
After implementing the OPEX® Sure Sort® automated sorting system:
-
- Labor requirements decreased by 45%, needing only 10-15 people for the order fulfillment process
- Order accuracy improved to an impressive 99.97%
- Boxes packed per hour increased from 26 to 40 (a 67% improvement)
- The system can sort up to 2,400 units per hour at maximum capacity
“We needed automation to keep up with customer demand. The Sure Sort system has enabled us to keep our same-day shipping promise to our customers.”
Scott McFarland,
Eastern DC Supervisor, Rocky Mountain ATV
Delta Galil: Reducing Labor by 50% While Processing 1,500 Items Per Hour
Delta Galil, a global leader in intimates and activewear, struggled with a manual sorting process that was time-consuming and inaccurate, which required extensive employee training. During peak seasons, Delta Galil needed 24 employees to operate its manual put wall system.
After implementing automated sorting technology:
- Labor requirements were reduced by 50%, from 12 employees per shift to just six
- New employee training time decreased from two weeks to just 15 minutes
- Order accuracy significantly improved, virtually eliminating errors common in manual sorting
“Just a few days after the installation, the huge difference in savings, accuracy, and intensity was very clear.”
Eran Gilboa,
VP of Logistics, Delta Galil
2. Enhancing Working Conditions and Safety
One of the most compelling benefits of warehouse automation is improving working conditions. By automating physically demanding tasks, companies can:
- Reduce repetitive motion injuries and physical strain
- Minimize the need for workers to lift heavy items
- Decrease walking distances and climbing requirements
- Lower accident rates related to manual material handling
ASRS delivers items directly to workers at ergonomic heights, reducing the physical strain associated with traditional warehouse jobs. This improves worker well-being and makes warehouse roles more attractive to potential employees, who focus on employee retention and satisfaction.
3. Shifting Workforce Composition Through Upskilling
While automation reduces the number of manual roles, it creates new opportunities in system operation, maintenance, and data analysis. Forward-thinking organizations are investing in up-skilling programs to help employees transition to these higher-value positions:
- System operators and automation specialists
- Maintenance technicians
- Inventory analysts and system optimizers
- Technology implementation and support roles
This transition to higher-skilled roles represents an evolution of warehouse work rather than its elimination.
This transition from manual labor to technical expertise positions warehousing as a more attractive career path for younger, tech-savvy workers, helping address long-term labor shortage concerns.
4. Space Optimization and Cost Efficiency
AS/RS systems can save up to 85% of floor space compared to traditional shelving, allowing companies to operate in smaller facilities or handle more inventory in existing spaces. This space efficiency translates to labor efficiency, as workers spend less time traversing the warehouse and more time on productive tasks.
Implementation Consideration for Operations Leaders
When considering automation solutions, several factors should guide implementation decisions, as illustrated by our case studies:
1. Start With a Strategic Assessment
Before investing in automation, conduct a thorough analysis of:
- Current and projected labor challenges
- Operational bottlenecks and inefficiencies
- Order profiles and storage requirements
- Return on investment calculations
Rocky Mountain ATV’s success began with a detailed analysis of their specific sortation challenges and SKU profile before selecting the right automation solution. Similarly, Boux Avenue discovered its automation solution after assessing how it would fit with the size and scale of its operation.
2. Adopt A Phased Approach
Rather than attempting a complete warehouse transformation, consider implementing automation in stages:
- Target high-volume, repetitive processes first
- Establish proof of concept with smaller implementations
- Scale successful solutions across the operation
3. Focus in Integration and Interoperability
Ensure new automation systems can integrate seamlessly with:
- Existing warehouse management systems (WMS)
- Enterprise resource planning (ERP) platforms
- Labor management and workforce optimization tools
4. Invest in Change Management and Training
Effective change management is critical to successful implementation:
- Communicate transparently about automation goals and timeline
- Address employee concerns about job security
- Develop comprehensive training programs for new roles
- Create career pathways for transitioning employees
Delta Galil’s experience highlights the importance of efficient training programs. With its automated system, Delta Galil reduced training time for new employees from two weeks to just 15 minutes. Similarly, Rocky Mountain ATV found that “training on the new sorting system was easy and enjoyable for employees and allowed them to get up and running quickly.”
Relevant Statistics
While automation addresses immediate operational challenges, industry leaders emphasize that human workers remain irreplaceable for certain aspects of warehouse operations:
The Human Advantage
- Complex problem-solving: Humans excel at addressing unusual situations and exceptions that automated systems can’t handle.
- Customer relationships: Person-to-person interactions remain essential for high-value accounts and complex service situations.
- Continuous improvement: Human insight drives innovation and process refinement beyond programmed algorithms.
- Adaptability: Humans can quickly adjust to changing priorities and unexpected circumstances.
Creating A Complementary Relationship
The most successful operations achieve synergy between automation and human talent:
- Automation handles routine, repetitive, and physically demanding tasks
- Human workers focus on exception handling, quality control, and customer service
- Technology augments human capabilities rather than replacing them
Measuring Success: KPIS For Balanced
To evaluate the effectiveness of automation implementations, operations leaders should track key performance indicators:
- Labor utilization rates: Measuring productivity per labor hour
- Order accuracy: Tracking error rates and quality metrics
- Throughput capacity: Monitoring volume processing capabilities
- Employee satisfaction: Assessing workforce morale and retention
- Training completion: Tracking upskilling and development progress
- Cost per order: Evaluating overall operational efficiency
- Space utilization: Measuring storage density and capacity
Future-Proofing Operations with ASRS Investments
Investing in automation technologies like ASRS and automated sorting systems isn’t just about addressing current labor shortages but building resilient operations capable of withstanding future disruptions.
Organizations that successfully implement these technologies gain:
- Operational flexibility: The ability to scale operations without proportional increases in labor
- Workforce stability: Reduced dependence on fluctuating labor markets
- Competitive advantage: Faster, more accurate fulfillment capabilities
- Sustainable growth: The foundation for continued expansion without staffing constraints
Conclusion
The most successful organizations view automation not as a replacement for human workers but as a strategic tool that allows their workforce to focus on higher-value activities. By automating repetitive tasks, improving working conditions, and creating opportunities for upskilling, companies can address labor shortages while building a more engaged, productive, and satisfied workforce.
As you consider your automation strategy, remember that the goal isn’t to minimize your human workforce – it’s to optimize it. Finding the right balance between technology and talent can create a resilient operation capable of thriving even in challenging labor markets.
Ready to learn more about how automation can help address your labor challenges? Contact our team of automation experts for a personalized consultation.
Other Resources You Might Find Helpful
Falcon+® Scanner Series
Georgia Department of Revenue Accelerates Processing Times By Automating The Open, Prep, And Scan Process
Scan2Archive Positioned To Embrace A Digital Future With The Solution From OPEX® And Smartech
Falcon® Scanner Demo
When Flatbed Scanning is NOT Enough
Claims Processing System No Longer Feels Like a Painful Root Canal
Enhancing the Digitization Process at Iron Mountain Government Solutions
Critical Efficiency Improvements in Document Management
OPEX® Falcon+® RED® One-Touch Scanning Envelope Opener
Portsmouth, VA Treasurer’s Office Goes from Cost Center to Revenue Center
NEXT LEVEL AUTOMATION
Unlock Operational Efficiency with OPEX
OPEX is powering the future of automation. Contact us to learn more about how our vertically integrated automated solutions can help take your business to new heights.