Green Warehousing: Sustainable Practices in Warehouse Automation
How Automated Warehouses Can Reduce Their Carbon Footprint
15 min read
60-Second Summary
Warehousing accounts for 11% of global CO₂ emissions, but automation offers a more sustainable solution. AI-driven logistics, energy-efficient AS/RS, self-charging robotics, and smart sorting systems reduce energy use, optimize space, and minimize waste. Automated fulfillment and electrified warehouse vehicles cut emissions, while allowing for real-time data tracking to improve efficiency. These innovations drive cost savings and sustainability, making automation essential for a greener, more profitable future.
Introduction
As global e-commerce and logistics grow, so does their environmental impact. Warehouses contribute significantly to carbon emissions through energy-intensive operations, excessive waste, and inefficient logistics processes. Studies indicate that warehousing and logistics account for nearly 11% of global CO₂ emissions.
Automated warehouse solutions offer a pathway toward greater efficiency, lower emissions, and a reduced carbon footprint. Implementing automation supports environmental goals and leads to long-term operational cost savings and increased productivity.
This eBook explores how warehouse automation can drive sustainability through energy efficiency, space optimization, waste reduction, and smarter logistics.
Chapter 1
The Environmental Impact of Warehousing
Warehouses are essential to global supply chains but have a substantial environmental impact. Energy consumption in traditional warehouses is highest in industrial sectors, primarily due to extensive lighting, numerous HVAC systems, and manual material handling equipment. This leads to high electricity bills and increased carbon emissions, which can account for roughly 15% of warehouse overhead. Traditional warehouses require vast real estate, often contributing to urban sprawl and deforestation. Poor space utilization means warehouses are operating inefficiently, underutilizing excessive square footage.
Another major concern is the excessive waste generated from packaging materials and the high rate of product mismanagement. Incorrect order processing leads to unnecessary returns, adding to transportation emissions and material waste. Inefficient fulfillment processes increase vehicle miles, fuel consumption, and greenhouse gas emissions. Warehouse operators can significantly reduce their environmental footprint and move toward sustainable logistics operations by addressing these challenges.
In the United States, the average non-refrigerated warehouse consumes approximately 6.1 kilowatt-hours (kWh) of electricity and 13,400 Btu of natural gas per square foot each year. Lighting and heating account for at least 76% of these usage figures.
Chapter 2
The Role of Automation in Green Warehousing
Automation plays a vital role in reducing the carbon footprint of warehouses by enhancing efficiency, minimizing waste, and optimizing energy use. Warehouses can leverage smart automation technologies and artificial intelligence (AI) to reduce excessive movement of goods and energy consumption.
Smart order fulfillment systems accurately process orders and reduce packaging waste and transportation-related emissions from returns or damaged goods. These combined benefits make warehouse automation a cornerstone of sustainable logistics.
Here are some key benefits of automated warehouse systems:
Energy Efficient Robotics: Automated storage and retrieval systems (AS/RS) and sorting systems can use self-charging, energy-efficient robots that consume significantly less power than traditional conveyor-based item handling.
Dense Storage Solutions: AS/RS allow for high-density vertical storage, reducing the footprint needed for storing inventory and allowing space to be repurposed.
Optimized Inventory Movement: Automated systems and AI-driven algorithms reduce excessive touches and movement, lowering energy usage.
Smart Order Fulfillment: Intelligent automation reduces packaging waste, decreases product damage and loss, enhances order accuracy, and speeds up shipments.
Case Study Insight: Kookaburra Educational Resources
Kookaburra implemented the OPEX Sure Sort system, reducing labor needs by 65% while improving sorting efficiency and reducing wasteful manual processes.
Chapter 3
Energy-Efficient Technologies in Warehouse Automation
Energy-efficient warehouse technologies are transforming the logistics industry by reducing power consumption while maintaining high productivity. AS/RS and other automated systems significantly reduce energy usage compared to traditional warehouse operations by minimizing unnecessary movement and optimizing inventory placement. Smart energy management systems also allow warehouses to capture and redistribute power efficiently.
Types of Energy-Efficient Automation Systems
Automated Storage and Retrieval Systems (AS/RS):
Implementing an AS/RS that increases storage density by nearly three times can significantly lower expected energy consumption, coming in at about half of the original estimate. Wireless robots within these storage solutions also feature real-time power management and braking energy recapture, reducing overall energy consumption. Eliminating traditional conveyor belts in favor of direct-to-operator tote retrieval further reduces energy waste by minimizing idle conveyor operations. AS/RS also minimizes labor requirements, lowering energy consumption.
Automated Sorting Systems:
Automated sorting systems promote sustainability by consuming less energy than autonomous mobile robots (AMRs), which require frequent recharging. They enhance sorting accuracy, reducing product returns and minimizing excess packaging. Additionally, these systems optimize logistics with precise shipments, decreasing the number of trucks needed. Minimizing labor requirements also contributes to fewer shifts and lower power consumption in facilities.
Other Energy-Efficient Solutions
Smart Lighting:
Smart lighting solutions, such as LED systems integrated with motion sensors, provide illumination only when necessary, reducing electricity consumption. According to US LED, LEDs use up to 75% less energy than conventional lighting, resulting in significantly lower utility bills. Automated warehousing systems allow for lights-out operations, meaning entire warehouse sections can run without full-time lighting, significantly reducing electricity use.
AI-Driven Climate Control:
AI-driven climate control optimizes HVAC operations, maintaining the ideal temperature with minimal energy use. Automated storage solutions allow for denser storage in a smaller footprint, which lowers climate control needs by reducing open-air temperature variations in large warehouse spaces. Modular racking designs keep stored inventory more compact, helping HVAC systems work more efficiently.
The transition to electric warehouse bots that operate on low-energy ultra-capacitor technology and self-charge in motion eliminates the need for excessive battery swaps or fossil-fuel-powered equipment. These energy-efficient solutions help businesses operate sustainably while reducing operational costs.
Case Study Insight: Bleckmann 3PL
By integrating Sure Sort with RFID scanning, Bleckmann doubled operational efficiency and reduced sorting errors, improving last-mile logistics sustainability.
Chapter 4
Sustainable Storage & Space Utilization
Traditional warehouses often require large footprints to accommodate their operations. However, sustainable automation solutions enable better space utilization through vertical dense-storage systems and optimized layouts. Warehouses can store more products in a smaller area, reducing the need for warehouse expansion and land use by implementing high-density racking and automated material handling solutions.
Intelligent storage solutions ensure that the inventory is organized efficiently, reducing travel time and improving order fulfillment speed. Advanced warehouse management systems (WMS) track inventory in real-time, preventing overstocking and ensuring optimal use of available space. This decreases waste and lowers overall energy consumption by reducing unnecessary material movement.
Key Benefits of Optimizing Warehouse Space:
High-density storage minimizes real estate expansion needs.
Reducing footprint lowers heating/cooling costs and emissions.
Maximized cubic storage leads to reduced material handling.
Chapter 5
Reducing Waste in Fulfillment & Packaging
Traditional warehouses often struggle with excessive waste due to inefficient packaging and inaccurate order fulfillment. Automation significantly improves sustainability by introducing intelligent packaging systems that optimize material usage, reducing waste. Automated packaging solutions can dynamically adjust the packaging size to fit items more efficiently, minimizing the use of unnecessary materials such as plastic wrap and cardboard.
Automating Order Packout and Takeaway
A major advancement in reducing waste within warehouse fulfillment is the integration of an automated pack-out and takeaway system. This solution automates the final stage of order fulfillment – retrieving and transferring sorted orders into their respective shipping containers – without requiring manual intervention, additional packaging materials, or unnecessary handling. These systems ensure that items are sorted and transferred efficiently, reducing the chance of packaging errors that often result in product returns and waste.
This one-touch automation system minimizes human handling, reduces damage to fragile goods, and eliminates the need for repackaging. The ability to process up to 1,800 units and extract 200 orders per hour ensures precise order sequencing and takeaway, leading to a leaner, more sustainable fulfillment process.
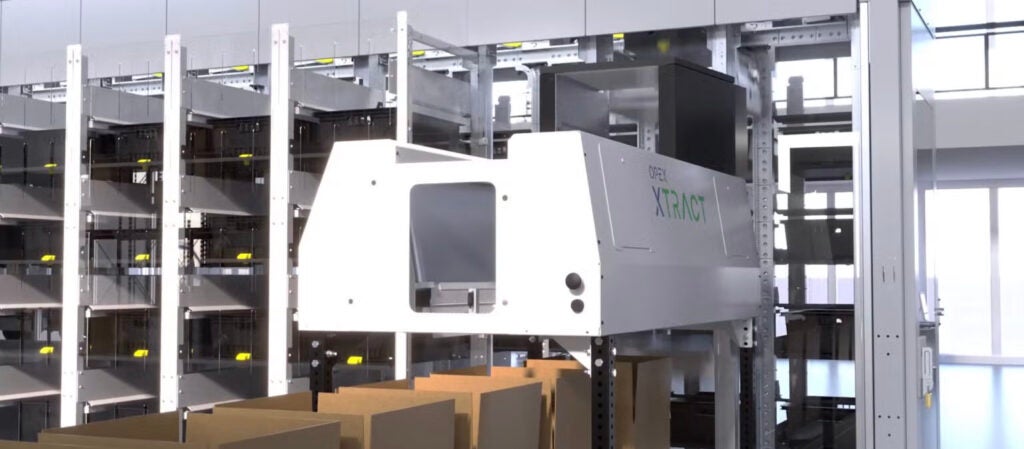
Beyond automation, recycling and circular economic initiatives are also critical in minimizing warehouse waste. Many companies are now designing packaging materials that can be reused, composted, or recycled efficiently. Automation enhances these efforts by streamlining waste sorting and optimizing the use of recyclable materials, making it easier for warehouses to implement closed-loop packaging systems. Companies can align their fulfillment processes with long-term environmental goals by integrating sustainable materials and reducing reliance on single-use packaging.
Chapter 6
Optimizing Logistics for Sustainability
Sustainable warehouse operations extend beyond the facility’s four walls – logistics and the supply chain play a crucial role in reducing carbon emissions and optimizing energy efficiency. Traditional fulfillment methods often rely on inefficient routing, excessive vehicle use, and outdated transportation management practices, leading to high fuel consumption and unnecessary emissions. Automation and data-driven logistics solutions transform how goods move through the supply chain, creating opportunities for warehouses to minimize their environmental footprint.
Methods to Reduce Environmental Impact in the Supply Chain
Warehouses can significantly reduce their carbon footprint, improve operational efficiency, and support a more sustainable logistics network by embracing automated sorting, electric warehouse vehicles, and real-time route optimization.
Implement Automated Sortation and Routing Systems:
One of the most impactful ways to reduce emissions is through automated sortation and routing systems. Leveraging intelligent sortation technology allows warehouses to group shipments efficiently and minimize the number of partially filled trucks leaving distribution centers. Automated sorting solutions enhance last-mile delivery efficiency by ensuring packages are correctly sorted and routed, reducing misrouted shipments that lead to extra fuel use and delivery delays. Shipment consolidation and distribution optimization directly contribute to lowering carbon emissions while improving customer satisfaction.
Transition to Electric Warehouse Vehicles and Robots:
Another key factor in sustainable logistics is transitioning to electric warehouse vehicles. Diesel-powered forklifts, pallet jacks, and autonomous guided vehicles (AGVs) contribute significantly to emissions within warehouse operations. Battery-powered forklifts and AGVs enable warehouses to cut emissions and reduce reliance on fossil fuels. Lithium-ion batteries, self-charging capacitors, and hydrogen fuel cell innovations make electric-powered warehouse vehicles more practical, offering longer operational times and faster recharging capabilities.
Utilize Analytics to Optimize Transportation
Real-time logistics data and route optimization are equally important in minimizing environmental impact. Many warehouses are now leveraging AI-driven transportation management systems (TMS) to analyze real-time delivery routes, reducing unnecessary mileage and improving fuel efficiency. Predictive analytics help determine the most efficient shipment schedules, enabling warehouses to combine deliveries and optimize truckloads, ultimately reducing emissions.
Chapter 7
Data Driven Sustainability in Warehouses
Data is the backbone of modern warehouse sustainability efforts. Without tracking and measuring energy consumption, material waste, and carbon emissions, warehouses cannot effectively implement and refine sustainability initiatives. Real-time data analytics and predictive sustainability tools enable warehouses to make data-driven decisions that enhance efficiency, reduce waste, and optimize resource allocation.
One of the most immediate benefits of real-time data tracking is its impact on energy efficiency. Sensors and IoT-enabled devices embedded within warehouse infrastructure allow businesses to monitor energy use in real-time, identify inefficiencies, and adjust operations accordingly. For example, smart warehouse management systems (WMS) can automatically regulate lighting and climate control based on occupancy levels, ensuring that energy is only consumed when and where needed. These smart energy solutions reduce electricity consumption and operational costs, making warehouses more sustainable and cost-effective.
The Role of Predictive Analytics
Beyond energy management, predictive analytics plays a crucial role in resource optimization. AI-powered forecasting tools can anticipate demand fluctuations, preventing overstocking and reducing waste from expired or unsold inventory. By analyzing historical sales trends and real-time consumer demand signals, warehouses can fine-tune their inventory levels, ensuring products move efficiently through the supply chain with minimal waste. Predictive analytics also supports proactive equipment maintenance, allowing facilities to schedule servicing before equipment failures occur, reducing downtime, and extending the lifespan of machinery.
Cloud-Based Performance Monitoring
A critical tool in optimizing sustainability and operational efficiency is a cloud-based platform that provides real-time machine performance monitoring, enabling warehouses to track key operational metrics and make informed decisions based on actual data. By consolidating and displaying performance data through interactive visualizations, these platforms allow businesses to monitor machine health, system throughput, and operational trends from anywhere. This real-time access to machine data helps warehouses reduce energy waste by optimizing equipment performance and identifying inefficiencies before they escalate into major disruptions.
Measuring Overall Equipment Effectiveness (OEE):
A good monitoring platform supports historical performance reporting, offering insights into overall equipment effectiveness (OEE) and throughput efficiency over time. OEE is a metric used to determine how efficiently equipment runs, considering machine availability, performance, and quality.
Leveraging this data enables warehouse managers to identify patterns, adjust workflows, and implement targeted sustainability initiatives that improve resource utilization and further reduce unnecessary energy consumption. Automated alerts and diagnostics help facilities maintain equipment proactively, reducing the likelihood of breakdowns that could lead to excess energy use or operational waste.
Another advantage of cloud-based monitoring system is its ability to deliver critical sustainability KPIs directly to operators and decision-makers. Metrics such as machine uptime, aisle availability, and performance benchmarks provide warehouses with the insights they need to improve their operations continually. With automated email reports and cloud-based dashboards, warehouse teams can quickly identify areas of inefficiency, optimize workflows, and reduce resource consumption.
Future-Proof Operations with Real-Time Data
By integrating real-time data tracking, predictive analytics, and sustainability performance metrics through platforms, warehouses can continuously improve their sustainability efforts, reduce costs, and enhance overall operational efficiency. The integration of data-driven decision-making not only supports long-term environmental goals but also creates more resilient and future-proof warehouse operations.
Chapter 8
ROI of Sustainable Warehouse Automation
Investing in sustainable, scalable warehouse automation provides significant financial and environmental benefits. Businesses can achieve a strong return on investment (ROI) by reducing energy consumption, labor costs, and waste. The key to measuring ROI is evaluating operational savings and efficiency improvements over time.
To assist with this calculation, we have provided an ROI calculator that helps warehouse managers assess the long-term benefits of automation. This tool factors in potential energy savings, reduced labor costs, and increased productivity to determine the payback period for automation investments.
Is Investing in Warehouse Automation Worth It?
Warehouses that implement automation see measurable improvements in efficiency, cost savings, and sustainability. The long-term financial benefits far outweigh the initial investment, making warehouse automation a strategic move for businesses focused on sustainability and profitability.
Example Calculation
Metric | Before Automation | After Automation | Savings |
---|---|---|---|
Annual Energy Cost | $200,000 | $140,000 | $60,000 |
Annual Labor Cost | $1,500,000 | $1,050,000 | $450,000 |
Annual Maintenance Cost | $100,000 | $140,000 | (-$40,000) |
Revenue Growth | - | +$500,000 | $500,000 |
Total Annual Savings | - | - | $970,000 |
Initial Investment | - | $2,000,000 | - |
Payback Period | - | 2.3 years | - |
ROI | - | 43% | - |
Conclusion
The Future of Sustainable Warehousing
The shift toward sustainable warehouse automation is not just about compliance – it’s about creating more efficient, cost-effective, and environmentally friendly operations. As automation technology evolves, warehouses will benefit from lower carbon footprints, optimized space utilization, and enhanced energy efficiency.
Reducing reliance on manual labor and traditional fossil-fuel-powered equipment enables companies to operate more sustainably while achieving long-term cost savings. AI-powered logistics, automated sorting, and sustainable packaging solutions lead the way toward an eco-friendly future. By embracing these innovations, warehouse operators can reduce waste, lower emissions, and improve overall efficiency.
The future of warehousing is one where automation and sustainability go hand in hand, ensuring businesses remain competitive while minimizing their environmental impact. Now is the time for industry leaders to implement sustainable automation.
Take the Next Step Toward a Greener, Smarter Warehouse
Other Resources You Might Find Helpful
NEXT LEVEL AUTOMATION
Unlock Operational Efficiency with OPEX
OPEX is powering the future of automation. Contact us to learn more about how our vertically integrated automated solutions can help take your business to new heights.