Starting Your Warehouse Automation Journey: What You Need to Know
A Practical Guide for Warehouse Operations and Supply Chain Professionals
22 min read
60-Second Summary
Warehouses today face growing challenges, from rising labor costs to increasing fulfillment demands and unpredictability, making efficiency more critical than ever. As automation shifts from a luxury to a necessity, many operations leaders ask, “Where do we start?” This eBook explores the key considerations for implementing automation successfully, from assessing your operations to making a business case for automated warehouse solutions. With real-world examples and industry benchmarks, this guide provides a clear look at both the opportunities and potential hurdles of automation, helping you make informed decisions that align with your operational goals.
Introduction
After years of disruptions, labor shortages, and supply chain bottlenecks, leaders realize that unpredictability is here to stay. The traditional manual warehouse model can no longer keep up with the demands of modern logistics, e-commerce, and ever-increasing customer expectations.
Automation has moved from a luxury to a necessity to stay competitive. E-commerce, next-day delivery expectations, and ongoing labor challenges have accelerated the adoption of automated solutions in warehouses worldwide. Companies that fail to modernize risk falling behind and cannot scale operations effectively for the future.
What This eBook Will Help You Understand
For companies considering warehouse automation, the journey can be daunting. How do you determine if your operation is ready? What are the most suitable technologies? How do you ensure successful implementation with minimal disruption?
This eBook serves as a comprehensive guide to starting your warehouse automation journey. Whether you’re looking for efficiency gains or exploring automation for the first time, this resource will help you:
- Identify operational pain points and assess your workflow.
- Navigate budgeting, implementation, and workforce transition strategies.
- Build a business case for automation and measure return on investment (ROI).
- Know the next steps to take in your automation journey.
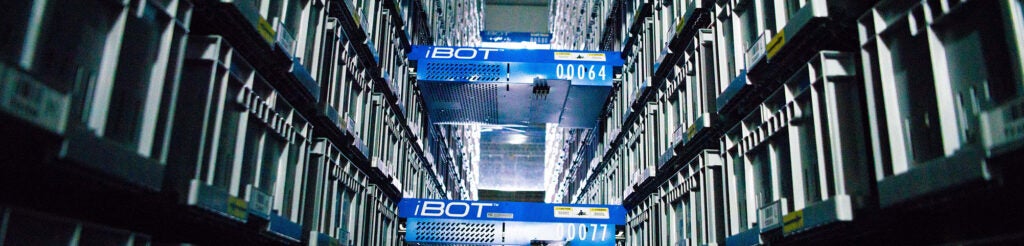
Chapter 1
Understanding Warehouse Automation
Before you take your automation journey, it’s crucial to understand the full range of automated warehouse solutions available in the marketplace. In this eBook, we’ll cover a few basic types of automation technologies.
Warehouse Automation: A Brief Journey
Warehouse automation uses technology to streamline warehouse operations, reduce manual labor, increase accuracy, and improve efficiency. It encompasses a wide range of solutions, from conveyors to robotic sorting systems and fully automated storage and retrieval systems (AS/RS). Solutions can be standalone or encompass a fully integrated and interconnected distribution center.
The Evolution of Warehouse Automation
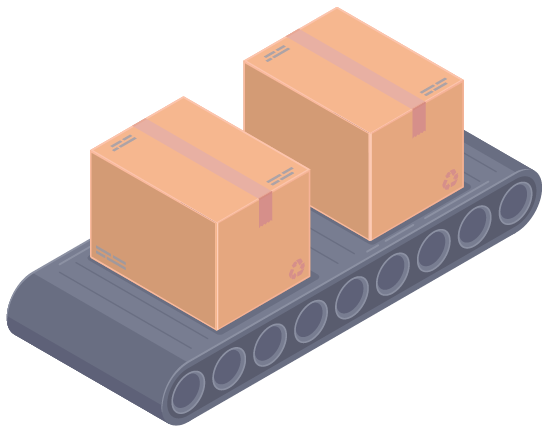
Warehouse automation has evolved significantly from its debut in the 1960s, from basic conveyor belts to AI-driven robotic fulfillment centers. Early automation efforts focused on mechanization and heavy pallet loads, while modern solutions incorporate machine learning, predictive analytics, and real-time data monitoring with complex robotics.
Common Types of Warehouse Automation Technologies
Automation solutions vary in complexity and scale. Here are some common types:
- Automated Storage and Retrieval Systems (AS/RS): AS/RS, the fastest-growing automation solution, is a high-density solution designed to store and retrieve goods quickly and efficiently. Inventory is stored securely in totes or trays within confined racking. Totes are then retrieved by robots or lift systems to deliver inventory to workers based on instructions from a warehouse management system (WMS) or order fulfillment software.
- Goods-to-Person Systems (G2P or GTP): A subset of AS/RS, a G2P system is the most popular type of AS/RS, focusing on automatically delivering goods directly to system operators.
- Automated Sortation Systems: These systems are designed to replace manual put walls, automatically identifying and sorting items based on pre-defined criteria.
- Autonomous Mobile Robots (AMRs): Robots that navigate warehouse floors independently without predefined routes, assisting with tasks like material transport and sorting. These robots can be used on both AS/RS and sortation systems.
- Automated Guided Vehicles (AGVs): Similar to AMRs, AGVs navigate warehouse floors but do so with defined or fixed paths to transport materials.
- Software: Many different types of software integrate with and power automated solutions to optimize inventory tracking, order fulfillment, and/or warehouse operations, including a WMS. When looking at software options, it’s crucial to consider an option compatible with new and existing systems.
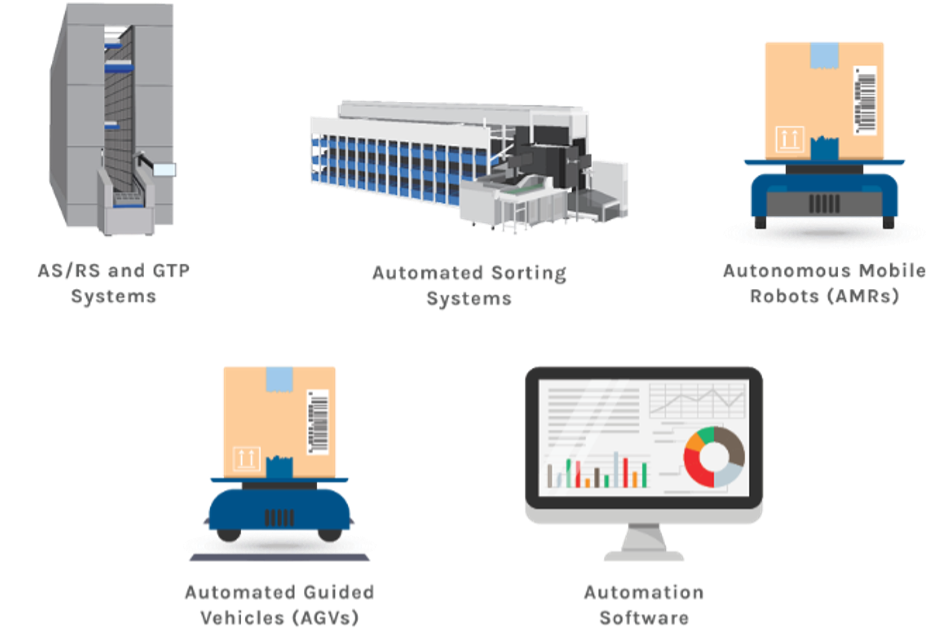
Widespread Misconceptions About Automation
Despite the clear advantages, misconceptions about automation persist, which makes it difficult for stakeholders to agree to invest in and implement a solution. Understanding automation misconceptions and how to navigate them will help you make the business case for automation.
“Automation will eliminate all jobs.”
In reality, automation helps warehouses reallocate existing labor to higher-value tasks, addressing labor shortages and the need for excessive temp staff rather than replacing workers entirely. Automation also enhances job opportunities by creating new roles focused on managing and optimizing technology.
“Automation is too expensive.”
While the initial investment can be significant in both capital and time, long-term savings and efficiency gains often justify the cost. Scalable solutions are available to make automation accessible to companies and warehouses of a variety of sizes.
“Automation is difficult to implement and integrate into my warehouse.”
With proper planning, phased implementation, and expert guidance from the right partner, automation can be integrated with minimal disruption. Modern automation solutions for seamless integration with existing warehouse systems are available and more widespread than ever.
“Integrating automation will cause too many disruptions and create downtime.”
While downtime and disruptions are possible, comprehensive planning and phased implementation are key to transitioning to an automated warehouse. Continuing manual and automated processes until the transition is complete will help limit disruptions. Preparing employees and pilot programs ahead of time will also help limit any surprises.
Chapter 2
Why Businesses Are Investing in Automation Technologies
Companies are turning to automation to solve pressing operational challenges, gain a competitive advantage, and reduce costs to improve profitability. This chapter explores the core reasons businesses invest in automation and how it impacts their bottom line.
Pressing Challenges That Make the Case for Automation
Businesses worldwide are moving towards automating operations due to many core challenges:
Labor Shortages and Rising Costs:
Companies struggle to find and retain skilled warehouse workers while dealing with high turnover. Wages aren’t only increasing but have become more competitive between companies as staffing shortages persist. This has made the overall cost of hiring employees significantly more expensive than in previous years. Automation empowers existing employees, increases efficiency, and boosts productivity, reducing the need for businesses to hire additional manual labor, especially during peak seasons.
Operational Inefficiencies:
Manual processes slow down fulfillment speeds, increase error rates, and lead to inconsistent performance. This can increase the cost of fulfillment and cause a business to lose customers as they look to competitors. Implementing automation helps to speed up fulfillment while reducing errors, leading to more consistent and reliable performance that consumers expect.
High Operational and Overhead Costs:
The overall cost of labor, real estate space, and the inefficient use of resources leads to high operational and overhead costs. Companies are investing in automation to mitigate these costs, lower risks, improve flexibility, and ensure continuity during disruptions.
Key Trends Driving Automation Adoption and Improvements
Industry leaders prioritize automation due to several emerging trends, with some companies re-evaluating and adjusting automation budgets to continue operational improvement.
Fulfill orders faster and exceed customer expectations:
Most companies surveyed by Modern Materials Handling (MMH) plan to evaluate or purchase automated solutions to fulfill orders faster and meet service-level agreements. (MMH)
Technological advancements:
Artificial intelligence (AI), robotics, and predictive analytics are gaining traction quickly, promising to make warehouse automation more intelligent, adaptable, fast-paced, and cost-effective than ever before. AI can also help with complex tasks and decision-making throughout the supply chain, helping to improve accuracy. (MHI)
Supply chain resilience:
Companies are investing in automation to mitigate risks, improve flexibility, and ensure continuity during disruptions. According to MHI’s 2024 Annual Industry Report, 55% of respondents have increased supply chain investments to ensure smoother operations. (MHI)
Reducing the need for additional manual labor:
Automation helps companies optimize their existing workforce while limiting the need for additional temp staff, saving labor costs. 44% of companies surveyed by MMH are looking to reduce labor in 2025. (MMH)
Empowering the existing workforce:
Automation enhances worker productivity by reducing repetitive and physically demanding tasks, allowing employees to focus on higher-value responsibilities. MHI’s 2024 Annual Industry Report found that 45% of respondents use technology to enable human decision-making, while 40% use it to empower human workers. (MHI)
Major Benefits of Warehouse Automation
Automation provides several advantages and benefits. Companies that invest in automation can experience the following:
- Increased Efficiency: Faster fulfillment and optimized workflows reduce processing time.
- Reduced Errors: Automated systems improve order accuracy and minimize human mistakes.
- Lower Operational Costs: Reduced reliance on manual labor lowers long-term expenses.
- Scalability: Warehouses can handle increased demand with little or no increased labor costs.
- Enhanced Workplace Safety: Reducing physical strain and repetitive tasks lowers workplace injuries.
- Improved Supply Chain Resilience: Automation enhances operational flexibility and adaptability to disruptions.
The warehouse automation market is expected to grow from $24.09 billion to $42.25 billion in 2034 at a compound annual growth rate (CGAR) of 15.1% due to the rise in same-day and on-demand delivery, sustainability, and e-commerce.
Chapter 3
Assessing Operations and Identifying Your Warehouse Needs
After researching the solutions available on the market, the next step is to assess your operations to figure out how these solutions can fit into your warehouse, distribution center, or supply chain.
Signs Your Warehouse is Ready for Automation
Automation is not a one-size-fits-all solution, and identifying the right time to invest is crucial. Here are key indicators that your warehouse may be ready for automation:
Rising labor costs and persistent staffing challenges:
Difficulty in hiring and retaining skilled labor can drive up operational costs and impact efficiency. Automated systems can accommodate fluctuations and shortages in labor.
Increasing order volume that exceeds manual capacity:
If your current workforce struggles to keep up with rising order demand, automation can help scale operations effectively without increasing headcount.
Frequent order inaccuracies and fulfillment delays:
Mistakes in order picking and shipping can lead to customer dissatisfaction, returns, and lost revenue. Automating these processes can remove human error, guiding staff to make fast, confident decisions.
Space constraints requiring improved storage efficiency:
If storage space is running low, limiting new inventory, or requiring extra real estate, automation can optimize existing warehouse space, allowing higher inventory density in the same footprint.
High customer demand for faster delivery times:
If you’re struggling to meet customer expectations for quick and accurate order fulfillment, automation can streamline the process, greatly raising productivity.
High operational downtime due to manual bottlenecks:
Delays caused by human-dependent processes can slow warehouse efficiency and impact profitability. Automation removes bottlenecks caused by manual processes and streamlines operations.
Conducting an Internal Workflow Audit
Before implementing automation, it’s essential to understand your current warehouse operations and identify areas for improvement. Conducting a workflow audit involves:
- Mapping Out Current Processes and Space: Documenting your warehouse workflows, from inventory receiving to order fulfillment, helps visualize inefficiencies and redundancies. Don’t forget to assess building readiness and the available space for automation.
- Analyzing Historical Order and Labor Data: Reviewing metrics such as order processing times, error rates, and labor costs provides insights into pain points and operational costs.
- Understanding Pain Points from Frontline Warehouse Staff: Engaging with employees who handle daily operations can reveal operational challenges and areas where automation could provide relief.
- Identifying Repetitive and High-Error Tasks: Automation is most beneficial in areas requiring repetitive tasks that are prone to human error, such as picking, sorting, and inventory handling.
- Evaluating Current Technology Integration: Assessing the compatibility of your warehouse management system (WMS) and/or enterprise resource planning (ERP) software ensures smooth integration with automation solutions.
Planning Your Warehouse for the Future
As warehouse needs evolve, investing in flexible and scalable automation solutions is essential for long-term efficiency. Planning for scalability with modular automation systems, which can expand gradually as business demands grow, can prevent costly overhauls. Seamless integration with existing infrastructure is equally important, as automation should enhance current workflows rather than disrupt them. Aligning automation investments with long-term business goals ensures that technology enhancements support strategic objectives, driving sustained growth and operational excellence.
Chapter 4
Choosing the Right Automation Solution
Selecting the right automation technology for your organization is crucial for long-term operational efficiency. This next chapter will explore financial planning and cost considerations for automation adoption.
Consider Your Warehouse Size and Inventory Profiles
Selecting the right automation solution depends on several factors, including order volume, SKU diversity, and available warehouse space. High-volume fulfillment centers with a large number of SKUs may benefit from an AS/RS to optimize storage, while smaller warehouses might find value in automated sorting systems to streamline item handling. However, automated solutions can provide a variety of benefits to a range of operations, making it critical to define your needs ahead of time.
Compare Vendors and Offerings
Choosing the right automation vendor requires careful consideration of key factors such as reliability, technology availability, and long-term support, such as service and maintenance. Businesses should assess vendors based on their ability to assist throughout the entire process, including analyzing workflows, planning, implementation, training, and support. Comparing cost structures, ongoing maintenance requirements, and the total cost of ownership will help determine the best investment.
When comparing vendors, evaluating case studies and customer testimonials in similar warehouse environments can provide valuable insights into a company’s reliability and performance. Ultimately, businesses should prioritize vendors that offer configurable solutions and strong customer support.
Prepare for Common Challenges
Businesses can maximize the success of their automation initiatives and ensure a seamless transition to a more efficient and scalable warehouse by planning for and addressing some common challenges:
Managing Workforce Adaption and Training:
One of the primary challenges is managing workforce adaptation and training. Employees may resist automation due to concerns about job security or difficulty adapting to new technology. To address this, businesses should proactively communicate the benefits of automation, provide hands-on training, and offer upskilling opportunities to help employees transition into more strategic roles.
Ensuring Minimal Downtime During System Deployment:
Another critical challenge is ensuring minimal downtime during deployment. Implementing automation without disrupting ongoing operations requires careful scheduling, phased rollouts, and contingency plans. Businesses can start with pilot programs or parallel testing to refine the integration before full-scale implementation, reducing operational disruptions.
Risk Management for Implementing Automation
Automation can provide great efficiency, but without risk management, it can introduce downtime, security issues, operational challenges, and more. Developing a proactive strategy allows businesses to minimize disruptions while further assessing which automation solution is the right choice.
Risk | Potential Impact | Mitigation Strategy |
---|---|---|
Integration Challenges | Compatibility issues with existing WMS/ERP systems. | Work with reputable vendors with on-site support and a proven integration track record. |
Downtime During Transition | Temporary disruptions to operations that limit fulfillment. | Use parallel testing environments before switching fully to automated systems. |
Cybersecurity and Interconnectivity Issues | Risk of data breaches, incomplete data, or synchronization issues. | Work with your IT Department and automation integrator to ensure all connected systems function properly and comply with network security standards. |
Employee Resistance | Low employee adoption rates, productivity loss, and operational slowdowns. | Conduct change management training, address concerns, and provide incentives for employees to learn automation systems. |
Hardware/Software Failures | Risk of bottlenecks, standstills, and downtime. | Implement preventive maintenance programs and redundant systems to prevent failures. |
Regulatory Compliance Issues | Violation of labor, safety, or data regulations that can pose hazards or penalties. | Ensure new systems comply with OSHA, GDPR, and local labor laws. Conduct compliance audits regularly. |
Scalability Limitations | Risk of investing in automation that doesnât scale, limiting future growth and output. | Choose modular and configurable automation solutions that can grow with warehouse demand and adjust to business needs. |
Chapter 5
Budget and Cost Considerations
Implementing an automation solution has several positive effects on warehouse operations, but the solution must be justified to decision-makers, especially in cost, budget, and ROI.
Understanding Long-Term Savings and ROI
Businesses can expect savings and efficiency gains in areas such as:
- Reduced Labor Costs: By automating repetitive tasks, companies can optimize workforce allocation and reduce dependency on manual labor.
- Improved Order Accuracy: Automation minimizes human error and inventory damage, leading to fewer returns and increased customer satisfaction.
- Higher Throughput and Efficiency: Automated solutions accelerate order processing and throughput with less labor, reducing cycle times and boosting overall productivity.
- Lower Operational Costs: Optimized workflows, lower resource use, and reduced energy consumption contribute to long-term cost savings.
- Scalability and Flexibility: Investing in modular automation solutions allows warehouses to scale operations without significant additional expenses or complete overhauls.
Calculating the ROI of a Warehouse Automation Project
One of the most important parts of your automation journey is calculating the ROI of an automation project. The ROI calculation is one of the keys to making your business case, helping to convince decision-makers to move forward with a project.
Additional Costs to Consider
When planning for automation, account for potential hidden costs that can impact the budget.
Customization and Software Upgrades:
Custom configuration of automation systems to specific features and workflows can increase expenses beyond initial estimates.
Maintenance and Spare Parts:
Automated systems require periodic maintenance and replacement parts, which can be costly. Determine if your integrator includes maintenance and spare parts as part of the agreement.
Cybersecurity, Data Management, and Software:
With increased reliance on automation and AI, investing in data security and compliance measures is essential. Additional software and integration may add to your budget.
Chapter 6
The Business Case for Warehouse Automation
Automation projects are a team effort. While Operations may take the lead, collaboration with your automation provider and other internal departments, including IT, Finance, and HR, are a must to successfully make a business case and move forward with the project.
Building a Strong Business Case for Automation
- Identify Key Pain Points: Highlight operational inefficiencies and areas where automation will have the greatest impact.
- Gather Supporting Data: Use industry benchmarks, case studies, and internal performance metrics to quantify potential benefits.
- Demonstrate ROI: Outline cost savings, increased productivity, competitive advantages, and payback.
- Create a Phased Implementation Plan: Provide a roadmap for gradual adoption to minimize risks and ensure success.
Overcoming Common Objections to Automation
Despite the benefits, some businesses hesitate to adopt automation due to common concerns or misconceptions. Addressing these objections is key to gaining internal buy-in from stakeholders.
High Upfront Costs:
While automation requires an initial capital investment, the long-term savings and efficiency gains should outweigh the expense. Clearly define and communicate an ROI and which areas will benefit from cost-savings.
Employee Displacement Fears:
Automation often lowers the need for manual labor, shifting workers to higher-value roles rather than replacing them entirely. It’s important to establish your business goals and determine if labor will be reallocated.
Integration Challenges:
Modern automation solutions are designed to integrate seamlessly with existing WMS and other software. However, it’s crucial to plan for the physical space requirements of your system(s) and any changes to your existing space.
Downtime During Implementation:
Phased deployment strategies can minimize operational disruptions and ensure a smooth transition during installation and integration. Work with internal stakeholders to establish how the system(s) are deployed.
Strategies for Securing Internal Buy-In and Budget Approval
Warehouse leaders must build a compelling case for stakeholders to gain approval for automation investments successfully. Key strategies include:
- Align with Business Goals: Highlight how automation supports company-wide objectives such as cost reduction, efficiency, competitive advantage, sustainability, or shipping guarantees.
- Present a Data-Driven Business Case: Use industry benchmarks, projected ROI, and cost-benefit analysis to demonstrate the value of automation.
- Address Stakeholder Concerns: Anticipate potential objections related to costs, workforce impact, and implementation, providing clear solutions.
- Starting with a Pilot Program: Demonstrating automation success on a small scale can help justify a larger investment.
A well-structured financial and implementation strategy ensures warehouse automation investments align with business objectives, paving the way for sustained operational efficiency and cost savings.
Boux Avenue, a leading UK lingerie and loungewear brand, transformed its order fulfillment operations by implementing OPEX’s
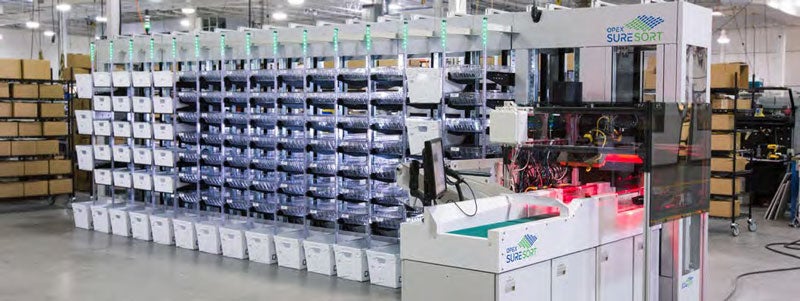
Boux Avenue enhances the order fulfillment process, reducing temporary labour by 33%
Sure Sort automated sorting system. The company faced peak-season challenges, including high temporary labor needs and increased operational strain. By integrating Sure Sort, Boux Avenue reduced temporary labor by 33%, streamlined order processing, and improved productivity. This automation significantly boosted efficiency during peak demand, accelerated order fulfillment, and enhanced customer satisfaction. As a result, Boux Avenue quickly realized a strong ROI and positioned itself for ongoing growth and operational excellence.
Conclusion
The Road Ahead
Warehouse automation is not just a trend; it is a fundamental shift in how supply chains operate. As businesses face labor shortages, rising costs, and increasing consumer demands, automation provides a viable path toward long-term sustainability and efficiency. Embracing technology and innovation positions businesses for continued growth with higher efficiency and operational excellence.
The Next Steps in Your Automation Journey
While the automation journey may seem complex, those who take a strategic approach will gain a competitive advantage in the evolving logistics landscape. For organizations considering warehouse automation, the next step is to assess their readiness and develop a roadmap for implementation.
Start by evaluating your pain points and workflows, setting clear objectives, and engaging key stakeholders. Whether beginning with a small pilot program or a full-scale deployment, having a structured approach ensures a smooth transition and maximum return on investment.
Now is the time to take the next step. Leverage the insights from this eBook and begin your warehouse automation journey with confidence.
Other Resources You Might Find Helpful
NEXT LEVEL AUTOMATION
Unlock Operational Efficiency with OPEX
OPEX is powering the future of automation. Contact us to learn more about how our vertically integrated automated solutions can help take your business to new heights.