From Bottlenecks to Breakthroughs: Optimizing Warehouse Operations with Technology
Orchestrating warehouse efficiency through automation
13 min read
60-Second Summary
Is your warehouse performing like a well-rehearsed symphony, or more like an orchestra warming up? In today’s high-pressure fulfillment environment, warehouse bottlenecks aren’t just frustrating – they’re profit killers. Manual processes, poor workflow design, and data invisibility are creating costly inefficiencies that impact your bottom line. This essential ebook reveals the hidden costs of warehouse bottlenecks and how to diagnose them before they cripple your operations. Don’t let bottlenecks hold your warehouse back from peak performance.
Introduction
Imagine a symphony where every instrument plays in perfect harmony. In an ideal warehouse, every process, from receiving to shipping, performs like a well-rehearsed ensemble with efficiency and precision.
Today’s warehouses face mounting pressures: rising labor costs, increasing order volumes, and the need for rapid fulfillment. Modern automation offers a solution that can re-tune your operations for peak performance, ensuring that every part of your supply chain contributes to a flawless performance.
This eBook explores how embracing automation can help you transform your warehouse into a symphony, where bottlenecks are minimized, and operations flow seamlessly.
Chapter 1
Understanding Warehouse Bottlenecks
Warehouse bottlenecks are the dissonant notes in an otherwise well-orchestrated performance. They disrupt the flow and can cause the entire system to falter, much like an off-key instrument in a symphony. These inefficiencies slow down order fulfillment and impact customer satisfaction and profitability. Recognizing and addressing these obstacles is the first step toward transforming your warehouse into a cohesive, high-performing ensemble.
Sources of Inefficiency
Inefficiencies often stem from outdated or manual processes that introduce delays and errors. For instance, manual sorting and picking force employees to traverse large spaces repeatedly, disrupting the operational rhythm much like a poorly timed rest in a musical piece.
Key Challenges Include:
- Manual Processes: Reliance on human labor for scanning, picking, and sorting increases error rates and slows operations. When each task is performed manually, even small delays can compound, leading to significant throughput issues.
- Poor Workflow Design: Inadequate layout and disorganized storage can result in excessive movement and redundant steps. Without a streamlined path, workers spend more time locating items rather than moving them efficiently.
- Data Invisibility: Without real-time data analytics, it becomes difficult to identify where bottlenecks occur. Managers may be unaware of issues until problems become severe, making reactive solutions less effective.
- Inconsistent Processes: Variability in how tasks are performed, from different shifts or teams, can lead to unpredictability in performance, creating sporadic delays that disrupt the overall flow.
“Automation gives us more capabilities and better throughput to support our customers.”
– Patrick Wedig, Director of Global Automation, Ingram Micro

The Impact of Bottlenecks
When bottlenecks occur, the entire symphonic performance suffers:
- Reduced Throughput: Every delay in sorting or picking slows down the entire process, limiting the number of orders that can be processed in a given timeframe.
- Increased Labor Costs: Labor costs increase when inefficiencies force workers to compensate for delays or correct mistakes. Over time, this erodes profit margins, leading to more reliance on temporary staffing during peak periods.
- Order Inaccuracies: Manual errors often result in mis-picks, affecting the speed of fulfillment, and lead to costly returns and decreased customer satisfaction.
- Underutilized Space: Inefficient storage practices lead to wasted space, limiting the warehouse’s capacity and flexibility to scale with growing demand.
Diagnosing the Problem
Diagnosing these issues is similar to fine-tuning an instrument before a performance. A thorough analysis of current operations—using key performance indicators (KPIs) like order accuracy, cycle times, and inventory turnover—provides the necessary insights to identify which parts of the process are off-key.
A Typical Diagnostic Process Involves:
- Mapping Workflows: Documenting every step of the order fulfillment process can help identify unnecessary delays. Visual process maps or flowcharts often reveal redundancies that can be eliminated.
- Tracking Performance: Implement technology to monitor real-time data and pinpoint delays—ensuring that every section of your warehouse plays in time.
- Soliciting Feedback: Direct input from floor staff can offer invaluable insights. They often have firsthand knowledge of the pain points and can suggest practical improvements that may not be immediately apparent from data alone.
By fully understanding these bottlenecks, you create the foundation for a more efficient, automated operation. When you address these inefficiencies, the entire system begins to operate more smoothly, much like a well-conducted symphony where every section plays its part flawlessly, contributing to a harmonious performance.
Chapter 2
The Promise of Automation
Warehouse automation is the conductor that can bring order to the cacophony of manual operations. Automation creates an environment where every operation is executed consistently and quickly by replacing manual processes with intelligent, continuous systems. This transformation is not simply about using new technology – it’s about fundamentally rethinking how work is done to maximize efficiency and drive better outcomes across the board.
When manual tasks are automated, the benefits extend beyond mere speed. For instance, automated systems are designed to work around the clock, ensuring peak performance is maintained even when human productivity might naturally wane. This continuous operation leads to increased throughput, meaning more orders can be processed in a shorter time frame.
Automation also plays a crucial role in reducing errors. Technologies like barcode and RFID scanning serve as the finely tuned instruments that keep every note precise, reducing mis-picks and minimizing costly errors.
Key Advantages of Automation Include:
Increased Throughput: Automated systems continuously process orders faster than manual methods, much like a symphony that seamlessly transitions from one movement to the next, drastically reducing cycle times and increases throughput.
Enhanced Accuracy: Technology-driven processes reduce human error. Consistent, accurate scanning and sorting ensure that each order is fulfilled correctly, minimizing the risk of mistakes that can disrupt the supply chain.
Optimized Labor Utilization: Automating repetitive and time-consuming tasks allows warehouse employees to focus on strategic and higher-value activities, similar to a soloist shining after the ensemble lays a solid foundation.
Improved Space Utilization: Automated storage solutions better utilize available space, organizing inventory to optimize every square foot. This efficiency is critical in warehouses where space is at a premium.
Operational Consistency: With automation, performance remains steady across all shifts, much like a symphony that delivers the same exquisite sound regardless of the conductor.
These benefits translate into a more streamlined, responsive, and cost-effective operation. Imagine a scenario where every product is quickly and accurately retrieved, sorted, and shipped without delays or errors inherent in manual processing. With the promise of automation, your warehouse can evolve from a source of recurring bottlenecks to a high-performance hub that reliably meets customer expectations and adapts seamlessly to growing demands.
The promise of automation is not a distant dream but a tangible opportunity to revitalize your warehouse operations. With careful planning and strategic implementation, automation lays the foundation for a future where efficiency is the norm, and every part of the process contributes to a harmonious and productive system.
Chapter 3
Orchestrating the Transformation: Harmonizing Sorting, Storage, and Implementation
To transform your warehouse into a symphonic masterpiece, you must reimagine sorting and storage, carefully navigating the implementation journey. Reimagining sorting and storage is about creating an environment where every item is in its optimal place and every process flows smoothly. It’s not just a theoretical concept—it’s a practical transformation that can redefine warehouse efficiency.
Equally important is the journey of implementing these changes, a process that requires thoughtful planning, collaboration, and a phased approach to ensure a seamless transition.
Reimagining Sorting and Storage
Imagine your warehouse as an orchestral score, where every product has a precise location and every movement is perfectly timed. Instead of chaotic, manual processes, envision an operation with:
- Efficient Inventory Organization:
Automated storage systems arrange inventory with the precision of a conductor directing each section. Every item is perfectly positioned, reducing search times, ensuring smooth transitions, and increasing overall throughput. Automated storage systems arrange inventory in high-density configurations, ensuring that every square foot is used effectively. - Intelligent Retrieval and Sorting:
Automated storage and retrieval systems (AS/RS) allow items to be located and brought to a picking station without delay, much like musicians seamlessly passing cues in a well-rehearsed piece. Advanced sorting systems use real-time data and intelligent algorithms to direct products accurately. Think of it as an automated sorting line that eliminates manual errors, significantly improving the speed and accuracy of order fulfillment. - Streamlined Workflows:
The reimagined process minimizes unnecessary steps and reduces physical strain on workers. Instead of manually scanning and moving items across long distances, automated systems guide each product to its destination swiftly and reliably.

Navigating the Implementation Journey
The journey to achieving this symphony of efficiency involves more than just installing new technology—it requires a strategic, phased approach that ensures every part of the transformation is in tune. Consider the following steps:
- Assessment and Planning:
Begin with a comprehensive analysis of your current operations. Map out existing workflows to identify key bottlenecks and inefficiencies, much like a conductor listens for dissonant notes before a performance. Use data to understand where delays occur and prioritize areas that need immediate improvement. This assessment acts as a blueprint for the transformation ahead. - Pilot Programs:
Before a full-scale rollout, conduct pilot tests in a controlled section of the warehouse. This allows you to observe the performance of new systems, fine-tune processes, and gather operator feedback. Pilot programs serve as a rehearsal, ensuring performance is as expected when the system goes live. - Phased Rollout:
Implement the new systems gradually. A phased approach minimizes disruption, as each segment of the warehouse transitions smoothly into the new model. This method also allows for adjustments based on real-time performance data, ensuring that any issues are addressed promptly without affecting overall operations, much like fine-tuning an instrument during a live performance. - Comprehensive Training and Change Management:
For the transformation to succeed, staff must be well-prepared to adopt new technologies. Develop detailed training programs with hands-on sessions, clear documentation, and ongoing support. Communicate the benefits of the new systems clearly, emphasizing how they will reduce workload, improve accuracy, and enhance overall operational efficiency. Think of this as ensuring every musician understands their part in the grand composition. - Continuous Monitoring and Improvement:
Even after the new systems are in place, the journey doesn’t end. Establish KPIs to monitor the system’s performance continuously. Regularly review these metrics and solicit feedback from staff to identify further improvements. This ongoing refinement is like a conductor continually guiding an orchestra to maintain peak performance.
Bringing It All Together
Reimagining sorting and storage, combined with a well-planned implementation journey, forms the cornerstone of a transformative warehouse strategy. By reorganizing the physical layout, integrating advanced retrieval and sorting technologies, and executing a phased implementation plan, you set the stage for an operation where efficiency is maximized and bottlenecks are a thing of the past.
This transformation is akin to completely overhauling an old building into a state-of-the-art facility. This process modernizes the space and optimizes every aspect of its operation. When each element works in unison, the entire warehouse operates with the precision and efficiency of a finely tuned machine.
Through a blend of innovative technology and strategic implementation, the promise of a reimagined warehouse becomes tangible. The journey may involve careful planning and incremental changes, but the result is a resilient, high-performing operation poised for future growth.
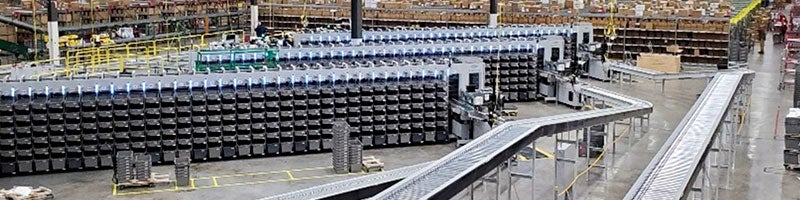
Chapter 4
Real-World Applications
Across industries, companies are transforming their operations by integrating advanced automation systems, and the results speak for themselves. For example, BioLegend reengineered its cold storage picking process by deploying the OPEX® Perfect Pick® AS/RS. This innovation accelerated order fulfillment and allowed employees to pick orders outside the cold room, ensuring efficiency and a safer work environment. The transformation led to faster processing and improved order accuracy.
Similarly, Bleckmann tackled the challenges of manual sorting by integrating an RFID scan tunnel with their OPEX Sure Sort® system. This upgrade doubled their sort rates and achieved an impressive 99% read accuracy, demonstrating how targeted automation can drastically enhance operational reliability and throughput in a high-volume environment.
Another compelling example is Newegg, which implemented a two-aisle OPEX Perfect Pick system to handle the peak-season surge in orders while maintaining strict security standards for high-value items. This strategic move enabled Newegg to achieve same-day shipping goals and manage exponential order volumes efficiently, showcasing the critical role of automation in supporting rapid growth.
These case studies illustrate that, when orchestrated correctly, OPEX systems can turn operational challenges into competitive advantages—delivering significant improvements in throughput, accuracy, and overall cost efficiency.
“The Perfect Pick system is part of the whole idea of this campus – to provide efficiency and enhanced customer service to our customers.”
– Bill Kullback, CFO, BioLegend
Conclusion
Unlocking the Symphony of Efficiency
The vision of a harmonious warehouse where every process contributes to a seamless performance is within reach. Through strategic automation, you can transform your operation from a congested, error-prone environment into an efficient, high-performing system. With carefully planned implementation and continuous improvement, your warehouse can achieve efficiency once thought impossible.
At the forefront of this transformation, advanced solutions such as OPEX Sure Sort X with Xtract™ feature with tote I/O option and the Infinity® AS/RS with tote I/O option stand ready to deliver. These state-of-the-art technologies ensure every order is fulfilled with the precision of a virtuoso performance, striking a perfect chord between speed, accuracy, and harmony.
Unlock Your Warehouse Symphony
Ready to transform your warehouse into a finely tuned symphony of efficiency? Take the next step and discover how automation can eliminate bottlenecks, boost throughput, and elevate your operational performance. Contact us today for a personalized consultation or to schedule a demo. Let us help you turn every process into a harmonious performance that drives success.
Other Resources You Might Find Helpful
NEXT LEVEL AUTOMATION
Unlock Operational Efficiency with OPEX
OPEX is powering the future of automation. Contact us to learn more about how our vertically integrated automated solutions can help take your business to new heights.