Boosting Efficiency and Cutting Costs: The Proven Benefits of Warehouse Automation
5 min read
60-Second Summary
As UK logistics face rising e-commerce demands, labour shortages, and the need for greater resilience, warehouse automation has become a strategic necessity. This blog explores how technologies like AS/RS, AMRs, and WMS/WCS systems can dramatically boost efficiency, accuracy, and throughput—while cutting labour and overhead costs. With proven ROI, real-world UK examples, and long-term scalability, automation isn’t just an upgrade—it’s a competitive advantage that smart businesses can’t afford to ignore.
Why Warehouse Automation is a Strategic Must for UK Logistics
The landscape of UK logistics is evolving at an unprecedented pace. From burgeoning e-commerce demands to ongoing labour challenges and the persistent need for supply chain resilience, businesses are under increasing pressure to do more with less. In this environment, warehouse automation isn’t just a buzzword; it’s a strategic imperative. For forward-thinking UK logistics and warehousing operations, embracing automation offers a clear path to significant efficiency gains and substantial cost reductions, ultimately delivering a powerful competitive advantage.
At its core, warehouse automation is about leveraging advanced technologies to streamline operations, minimise manual intervention, and optimise resource utilisation. It’s about moving beyond traditional, labour-intensive processes and embracing intelligent systems that work faster, more accurately, and around the clock. The benefits are not theoretical; they are tangible and measurable, directly impacting a company’s bottom line.
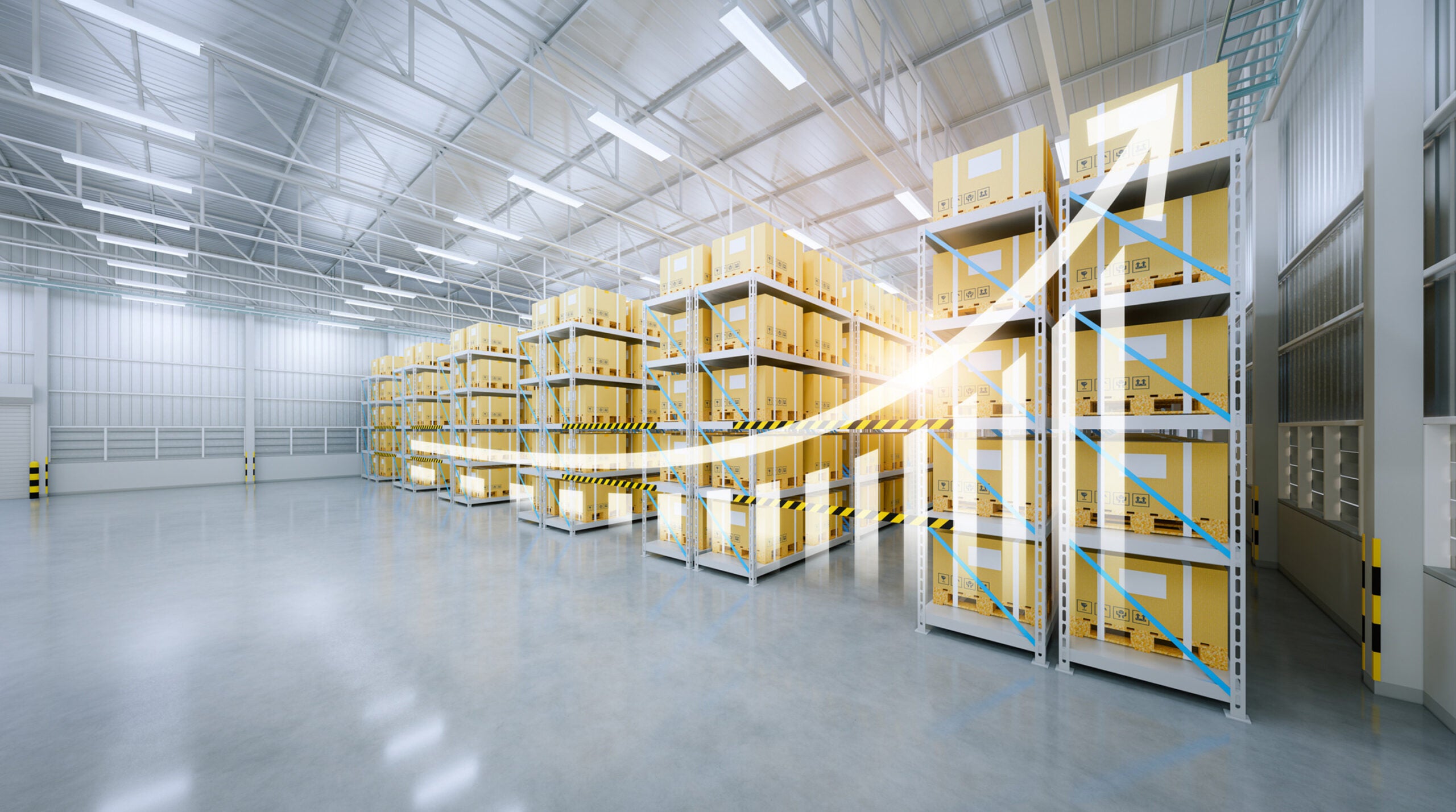
Super Charging Throughput: How Automation Drives Operational Efficiency
One of the most immediate and impactful benefits of warehouse automation is the dramatic improvement in operational efficiency. This isn’t just about moving products more quickly; it’s about optimising every single touchpoint within the warehouse.
- Faster Processing and Throughput: Automated systems, such as automated storage and retrieval systems (AS/RS) and goods-to-person robotics, can pick, sort, and move inventory at speeds far exceeding manual operations. This directly translates to increased throughput, enabling warehouses to process a higher volume of orders in less time. For UK businesses grappling with peak seasons or rapid growth, this enhanced capacity is invaluable. Imagine the difference during Black Friday or the run-up to Christmas, where automated systems can effortlessly handle surges in demand, ensuring timely deliveries and satisfied customers.
- Reduced Handling and Travel Times: Traditional warehouses often involve significant human travel time between storage locations Automated guided vehicles (AGVs) and autonomous mobile robots (AMRs) eliminate this wasted effort, transporting goods directly and efficiently. This not only speeds up operations but also reduces wear and tear on equipment and infrastructure, further contributing to efficiency.
- Optimised Space Utilisation: Automation allows for denser storage solutions. AS/RS systems, for instance, can utilise vertical space much more effectively than manual setups, often reducing the physical footprint required for a given volume of inventory. In a country like the UK, where prime warehouse space can be at a premium, this maximised use of existing facilities can lead to substantial savings and defer the need for costly expansions.
- Improved Inventory Accuracy: Manual inventory management is inherently prone to errors. Automated systems, integrated with robust Warehouse Management Systems (WMS), provide real-time, highly accurate inventory data. This precision minimises misplaced stock, reduces stockouts, and enhances order fulfilment rates, leading to fewer customer complaints and returns.
- Enhanced Order Fulfilment Accuracy: Automation significantly reduces human error in picking and packing. Robotic picking systems, guided by sophisticated software, ensure that the right product is picked every time, leading to near-perfect order accuracy. For UK consumers, who expect flawless and fast deliveries, this level of accuracy is a significant differentiator.
Cutting Costs: The Financial Payback of Automation Investment
While the initial investment in warehouse automation might seem significant, the long-term cost savings are compelling and often provide a rapid return on investment (ROI). These savings stem from various operational efficiencies and reduced dependencies.
- Reduced Labour Dependence: Automation can significantly reduce the reliance on manual labour for repetitive or strenuous tasks. This doesn’t necessarily mean eliminating jobs entirely, but rather redeploying human talent to more strategic, higher-value activities within the warehouse, such as supervision, maintenance, or data analysis. For UK businesses facing ongoing labour shortages and rising wage costs, this offers a sustainable solution to operational expenses.
- Lower Operational Overheads: Beyond direct labour costs, automation reduces other operational overheads. Less human movement can mean reduced energy consumption for lighting and heating in certain areas. Furthermore, the precision of automated systems can lead to less product damage and fewer errors, cutting down on waste and rework costs.
- Minimised Error Rates and Returns: Every picking error or damaged item carries a cost – from repacking and reshipping to handling returns and customer service. Automated systems dramatically reduce these errors, leading to fewer returns, lower customer service costs, and ultimately, a healthier bottom line. The impact on customer satisfaction, while harder to quantify in monetary terms, is equally significant.
- Optimised Energy Consumption: Modern automated systems are designed with energy efficiency in mind. Intelligent software can optimise routes for AGVs and AMRs, and AS/RS systems can be engineered for minimal power draw, contributing to lower utility bills – a welcome relief for UK businesses grappling with rising energy prices.
The Foundational Role of WMS and WCS
It’s crucial to understand that the full benefits of warehouse automation are unleashed when technologies are orchestrated by intelligent software. Warehouse Management Systems (WMS) and Warehouse Control Systems (WCS) are the brains behind the brawn of automation.
- Warehouse Management System (WMS): A WMS acts as the overarching intelligence, managing inventory, orders, and overall warehouse operations. It directs where products are stored, how orders are picked, and manages the flow of goods. A robust WMS is essential for optimising space, streamlining processes, and providing real-time visibility into inventory. For UK businesses, a WMS allows for seamless integration with enterprise resource planning (ERP) systems, providing a holistic view of the supply chain.
- Warehouse Control System (WCS): A WCS sits below the WMS, directly controlling the automated equipment on the warehouse floor. It takes commands from the WMS and translates them into instructions for conveyors, robots, AS/RS, and other automated machinery. The WCS is critical for ensuring that all automated components work together cohesively and efficiently, maximising throughput and minimising bottlenecks.
Together, WMS and WCS ensure that automation is not just a collection of machines but a unified, intelligent system that continuously optimises operations for peak efficiency and cost-effectiveness.
Real-World Impact: Illustrating the ROI in the UK
Consider a mid-sized UK e-commerce fulfilment centre processing thousands of orders daily. Manually, this would require a significant workforce, substantial walking distances, and an inherent risk of picking errors. By implementing an AS/RS system for storage and a fleet of AMRs for picking and transportation, the centre could:
- Increase picking speed by 200-300%: Dramatically reducing order cycle times.
- Reduce labour costs by 30-50%: Reinvesting in training for higher-skilled roles or coping with labour shortages.
- Improve order accuracy to 99.9%: Leading to fewer returns and higher customer satisfaction.
- Optimise warehouse footprint by 15-20%: Avoiding the need to acquire additional, costly commercial property.
These are not isolated examples; they represent the tangible benefits that UK businesses are already realising by embracing intelligent automation solutions. The initial investment is quickly recouped through a combination of increased revenue from higher throughput, reduced operational expenses, and enhanced customer loyalty.
The Path Forward: Embracing Automation for UK Logistics Success
For UK logistics and warehousing businesses, the question is no longer if to automate, but when and how. The proven benefits of increased efficiency and significant cost reductions are too compelling to ignore. Automation provides the resilience, scalability, and competitive edge necessary to thrive in today’s dynamic market.
It’s about making smart, data-driven decisions that position your operation for long-term success. By understanding how automation directly contributes to improved throughput, reduced errors, optimised space, and lower operational costs, you can build a compelling business case for investment.
Ready to delve deeper into the financial analysis and see real-world examples of success? Visit “The Definitive Guide to Warehouse Automation in the UK” for detailed case studies, practical insights into calculating your potential ROI, and a comprehensive overview of how to build a robust business case for automation in your UK operation. Schedule a meeting
Other Resources You Might Find Helpful
When to Outsource versus Invest in In-House Scanning Technology
Navigating the Pitfalls: Addressing the High Costs and Cybersecurity Risks of Warehouse Automation
The Power of Partnership: Collaborating for Supply Chain Optimization and Growth
Smarter Planning, Smoother Operations: Overcoming Forecasting and Coordination Challenges
Navigating the UK Logistics Workforce: Strategies for Resilience and Growth in an Automated Era
Understanding the Impact of Staff Shortages in Warehouses and Distribution Centres
Developing Leaders: Why Succession Planning is Key to Long-Term Success in Logistics
Enhancing Warehouse Efficiency: Leveraging Software and Systems for Peak Performance
Investing in Sustainability: Addressing the Cost Barrier and Seeking Government Support
Building A Greener Supply Chain: The Role of Sustainability
NEXT LEVEL AUTOMATION
Unlock Operational Efficiency with OPEX
OPEX is powering the future of automation. Contact us to learn more about how our vertically integrated automated solutions can help take your business to new heights.