SMARTER PLANNING, SMOOTHER OPERATIONS: OVERCOMING FORECASTING AND COORDINATION CHALLENGES
5 min read
60-Second Summary
Disjointed teams, inaccurate forecasts, and poor supplier coordination often undermine even the most advanced warehouse technologies. Smarter planning and tighter communication across departments and partners are key to improving efficiency, reducing costs, and staying ahead of demand. From integrated dashboards to real-time coordination tools and AI-powered forecasting, the right strategies help warehousing operations in the UK run smoother, adapt faster, and deliver better results.
Introduction
Many UK logistics businesses with logistics operations in the UK have invested heavily in automated storage and retrieval systems (AS/RS), robotic sorters, and conveyor systems. Yet despite this, operational headaches persist. Why? The real difference between a warehouse that runs like clockwork and one constantly putting out fires often comes down to planning and coordination. If teams are misaligned or working off inaccurate forecasts, even the most advanced technology will struggle to deliver results. Planning isn’t just a back-office function; it’s the heartbeat of warehouse operations. Without it, productivity drops, costs rise, and customer satisfaction takes a hit. The good news? These challenges are solvable.
By rethinking how you forecast demand, communicate across teams, and collaborate with partners, you can unlock smoother operations, fewer surprises, and a far more resilient business. Below,In this article, we outline five key areas to target. —and fFor a more detailed guide, head to our operations hub on strategy and cost control.
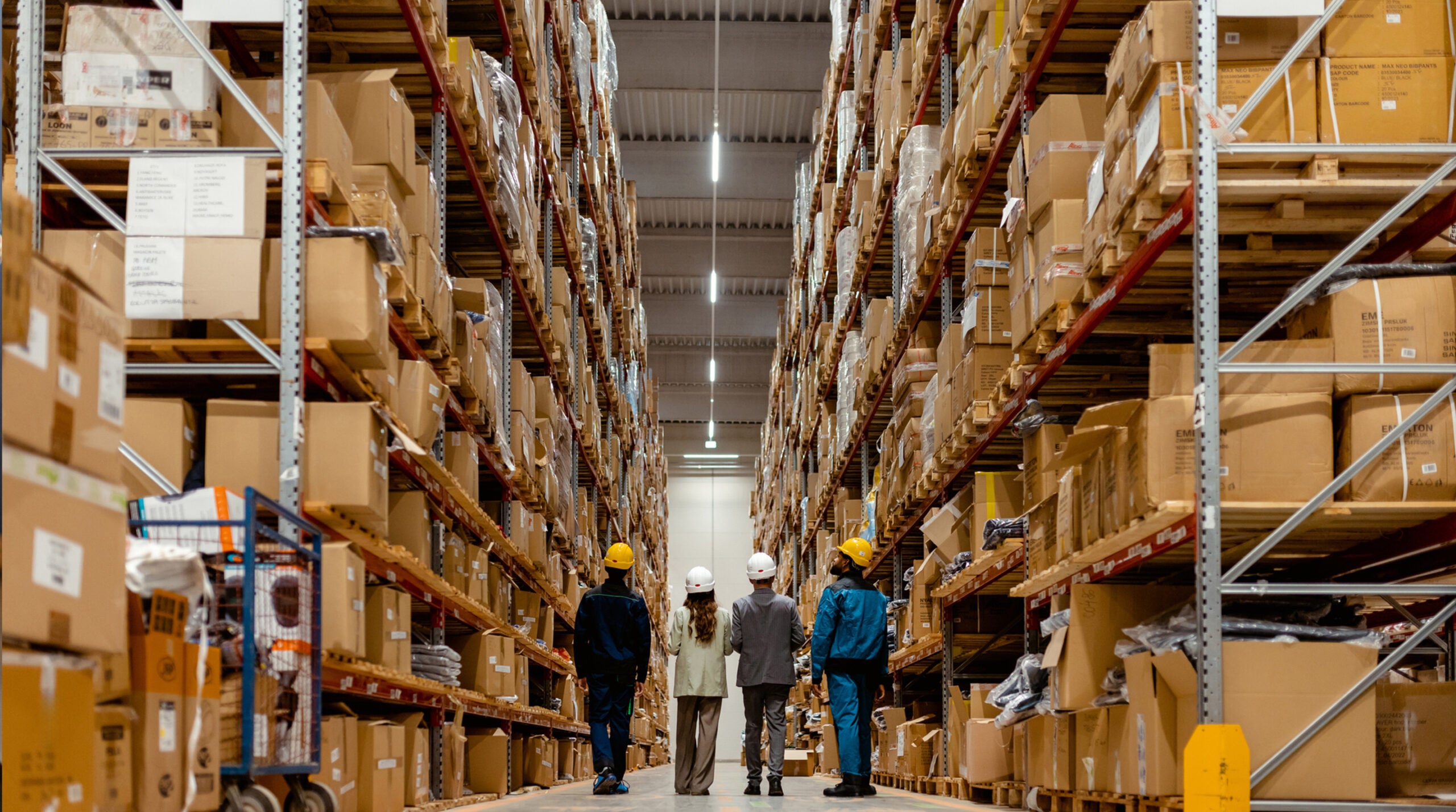
Overcome Siloed Decision-Making
Too many warehouses still operate with fragmented systems and disjointed departments. Sales, procurement, transport, and warehouse teams often work in silos, chasing different targets using data that may be incomplete or outdated. This lack of alignment leads to inefficiencies: stock levels fluctuate unpredictably, shipments get delayed, and customer service suffers. A common example is when transport teams are caught off guard by a sudden spike in outbound volume that sales knew were coming but didn’t communicate. These problems are preventable. Adopting a centralised planning platform or shared dashboards across departments ensures everyone is working from the same playbook. Real-time data integration means warehouse and transport teams can respond immediately to shifting demand or disruptions. These tools create transparency, improve agility, and foster collaboration, which reduces risk and supports more strategic decision-making across the entire supply chain.
Improve Forecasting Accuracy
Forecasting is a linchpin of warehouse performance, yet many operations still rely on spreadsheets or static ERP reports that don’t reflect the pace or complexity of modern commerce. Errors in forecasting ripple through every area: too much stock results in wasted space and capital and too little leads to stockouts and missed sales. Inaccurate forecasts also impact staffing, making it harder to allocate labour effectively or plan shifts during peak times.
Modern forecasting tools can help by:
Using AI and machine learning to identify trends and seasonality
Integrating with your WMS to align forecasts with real-time inventory levels
Providing dynamic updates as demand patterns shift
The result? Fewer surprises, better service levels, and reduced operational costs.
Adopt Sales and Operations Planning (S&OP)
S&OP may sound like corporate jargon, but its impact on warehouse performance is very real. Without regular cross-functional alignment, warehouse managers are often left reacting to shifting sales plans, unpredictable order volumes, or last-minute marketing campaigns. This reactive mode leads to inefficiencies such as urgent stock movements, missed delivery slots, and increased labour costs. Regular S&OP meetings create a space where leaders from sales, operations, logistics, and procurement can come together to align on forecasts, capacity, and resources.
By making trade-offs visible and agreeing on shared priorities, businesses can reduce the chaos that often accompanies promotional surges or seasonal peaks. S&OP isn’t just about planning; it’s about trust, accountability, and transparency. When everyone understands the plan, and contributes to building it, it becomes much easier to execute it. The result is fewer firefights, better customer outcomes, and a warehouse that’s prepared for what’s coming next, not just reacting to what just happened.
Tighten Internal Workflows
A lack of coordination within the warehouse can derail even the most carefully laid plans. Poor task visibility, manual handovers, and communication gaps between teams lead to delays, errors, and finger-pointing when things go wrong. These workflow inefficiencies waste time, drive up labour costs, and increase the risk of late or incorrect shipments. Fortunately, warehouse-specific coordination tools are making it easier to stay in control. These systems allow supervisors to assign tasks, track progress in real time, and escalate issues as soon as they arise. When every department, from receiving to shipping, has visibility into what’s happening, teams can respond faster and work more effectively together. Automated alerts, digital checklists, and mobile interfaces reduce reliance on paper or walkie-talkies, helping staff stay focused on execution rather than firefighting.
Streamlining internal workflows doesn’t just make life easier for your team, it creates a stronger, more responsive warehouse capable of handling whatever the day throws at it.
Coordinate with Suppliers and 3PLS
Misalignment with suppliers and logistics partners is a common source of disruption. Late inbound deliveries, inaccurate advance shipping notices (ASNs), or confusion about storage capacity at a 3PL facility can quickly create bottlenecks. Without shared data and clear communication channels, it’s difficult to plan inbound flows, allocate space, or ensure timely loading and dispatch.
Improved coordination with external partners can deliver:
- Fewer inbound surprises thanks to accurate ASNs
- Better planning through shared access to order and inventory data
- Greater dock efficiency and transport readiness at 3PL sites
When your extended supply chain is aligned, your warehouse runs smoother, your teams stay focused, and your customers benefit from more consistent and reliable service.
Strategic Planning Starts Here
Planning and coordination challenges don’t resolve themselves. They require deliberate effort, smart tools, and clear communication. But the payoff is significant: fewer delays, reduced costs, improved service, and a more confident, agile operation. If your forecasts aren’t delivering or your teams are working at cross purposes, now’s the time to course correct.
Discover how to transform your warehouse operations from reactive to proactive in the complete guide, Optimising Operations: Strategies for Efficiency and Cost Control, for more insights tailored to the UK warehousing landscape.
Want to learn more? Contact us to schedule a meeting or demo today.
Other Resources You Might Find Helpful
Optimising Operations: Strategies for Efficiency and Cost Control in UK Logistics
Developing Leaders: Why Succession Planning is Key to Long-Term Success in Logistics
Investing in Your Team: Proven Strategies to Improve Pay, Conditions, and Staff Wellbeing
The Power of Partnership: Collaborating for Supply Chain Optimization and Growth
Record Partners Provides High-Volume Critical Record Digitisation with New Technology
The Definitive Guide to Warehouse Automation in the UK
Enhancing Warehouse Efficiency: Leveraging Software and Systems for Peak Performance
Why ESG Matters: Meeting Customer Expectations and Enhancing Corporate Reputation
Which Automation Technologies are Right for Your Warehouse? An Overview of AGVs, AMRs, and More
Right-Speed Scanning: Revolutionising Document Processing Efficiency
NEXT LEVEL AUTOMATION
Unlock Operational Efficiency with OPEX
OPEX is powering the future of automation. Contact us to learn more about how our vertically integrated automated solutions can help take your business to new heights.