The Definitive Guide to Warehouse Automation in the UK
A Comprehensive Resource for Modern Logistics and Warehousing Businesses
14 min read
60-Second Summary
The UK warehousing landscape is undergoing a fundamental transformation. E-commerce growth, persistent labour challenges, and evolving customer expectations have made automation a strategic necessity rather than a luxury. Post-Brexit labour dynamics, rising operational costs, and the demand for same-day delivery have created the perfect storm for the adoption of automation.
This guide explores warehouse automation, from foundational technologies to strategic implementation, addressing the unique needs of both large enterprises and small to medium-sized enterprises (SMEs). We’ll examine market trends, implementation challenges, and emerging technologies that’ll shape the future of UK warehouse operations.
Chapter 1
Understanding Warehouse Automation
Definition and Scope
Warehouse automation encompasses technology, machinery, and software systems that perform tasks traditionally carried out by human workers. This ranges from simple, mechanized processes to sophisticated autonomous systems that operate with minimal human intervention.
Modern automation creates intelligent, data-driven environments that adapt to changing demands, optimize performance in real-time, and provide unprecedented operational visibility.
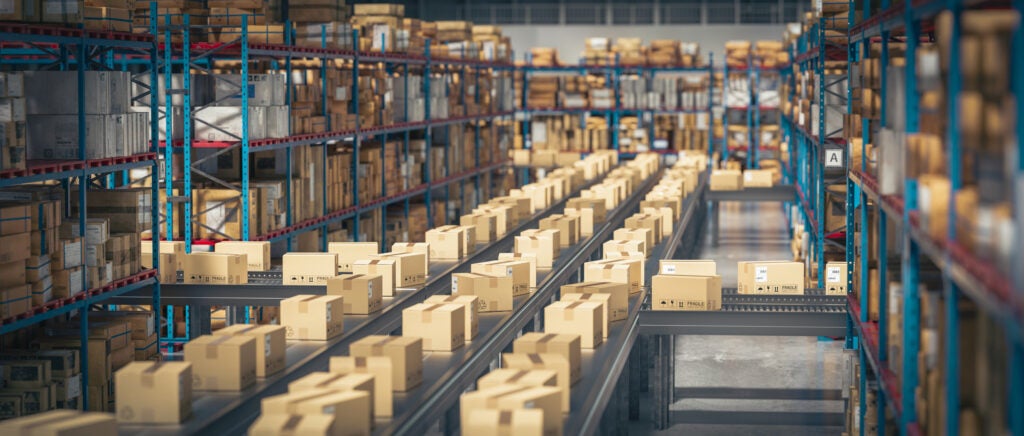
Why Automation is Critical in the UK Market
Labour Shortages and Skills Gaps
Brexit’s impact on the logistics sector created immediate staffing pressures. The initial exodus of approximately 125,000 EU workers, combined with ongoing recruitment difficulties and an aging workforce, continues to challenge operations. Automation directly addresses these issues by reducing dependence on manual labour for routine tasks.
E-commerce Growth and Customer Expectations
E-commerce now accounts for over 30% of UK retail sales, significantly altering warehouse requirements. Same-day and next-day delivery expectations require processing speeds and consistency that manual operations cannot match at scale.
Rising Operational Costs
Increasing labour costs, higher property values, and energy price volatility have squeezed margins. Automation offers improved cost efficiency through reduced labour dependency, better space utilization, and optimized energy consumption.
Levels of Automation
Level 1: Basic Mechanization – Simple mechanical aids like powered conveyors and pallet jacks that reduce physical strain.
Level 2: Semi-Automation – Systems combining human workers with technology, including pick-to-light systems and voice-directed picking.
Level 3: Advanced Automation – Robotics and intelligent systems like AGVs, AMRs, and robotic picking systems that operate with minimal human intervention.
Level 4: Full Automation – Systems operating with minimal human oversight, including lights-out warehouse sections.
Level 5: Cognitive Automation – AI and machine learning systems that learn, adapt, and optimize themselves continuously.
Chapter 2
Key Automation Technologies in the UK
Automated Guided Vehicles (AGVs) and Autonomous Mobile Robots (AMRs)
- AGVs follow predetermined paths using magnetic strips or laser guidance, excelling in predictable workflows and heavy load handling. They’re ideal for manufacturing and distribution centres with consistent, high-volume movements.
- AMRs use sensors, cameras, and AI to navigate dynamically through warehouse environments. Their flexibility makes them perfect for varied layouts common in UK warehouses. AMRs can work collaboratively with humans, adapting routes in real-time and bringing products to pickers rather than requiring the picker to travel.
Automated Storage and Retrieval Systems (AS/RS)
AS/RS addresses space maximization in expensive UK real estate markets, utilizing computer-controlled mechanisms to place and retrieve loads automatically.
- Mini-Load Systems: Handle small parts and totes, ideal for e-commerce operations
- Unit-Load Systems: Manage full pallets for distribution centres
- Vertical Lift Modules: Maximize vertical space in height-restricted facilities
Conveyor and Sorting Systems
Modern conveyor systems incorporate variable speed controls, sorting capabilities, and warehouse management system (WMS) integration. Advanced sortation systems, including cross-belt, shoe, and split-tray sorters, can process thousands of items hourly with exceptional accuracy.
Robotics Applications
- Articulated Robots: Excel in palletizing operations with continuous performance
- Collaborative Robots (Cobots): Work safely alongside humans with lower costs and easier programming
- Vision-Guided Robots: Handle complex tasks like bin picking and quality inspection
AIDC Technologies
- Barcode Systems: Reliable and cost-effective with 2D capabilities
- RFID Technology: Enables automatic identification without line-of-sight scanning
- Vision Systems: Read multiple codes simultaneously and detect quality issues
Software: The Intelligence Layer
- Warehouse Management Systems (WMS): Central coordination of inventory, orders, and resources
- Warehouse Execution Systems (WES): Real-time optimization across multiple automation technologies
- Warehouse Control Systems (WCS): Direct equipment control and coordination
Chapter 3
Benefits of Warehouse Automation
Operational Efficiency Improvements
Automation eliminates bottlenecks, reduces cycle times, and enables continuous operation. Automated sorting systems process thousands of items per hour, while AMRs reduce picking travel time by up to 70%. Systems can operate 24/7 and scale performance rapidly during peak periods.
Labour Cost Reduction
Beyond direct cost savings, automation reduces recruitment and training expenses while enabling the reallocation of the workforce to higher-value activities. This improves job satisfaction and reduces dependency on temporary labour during peaks.
Accuracy and Error Reduction
Automated systems achieve near-perfect accuracy levels. Vision-guided systems achieve accuracy rates exceeding 99.9%, while RFID tracking maintains real-time inventory accuracy, reducing safety stock requirements and enhancing demand planning.
Enhanced Safety
Automation reduces manual handling injuries, improves ergonomics, and enables operations in hazardous environments. Consistent execution of safety protocols reduces accident risks caused by human error.
Space Optimization
AS/RS systems achieve 40-60% higher storage density than conventional racking by eliminating aisles and maximizing vertical space. Dynamic space allocation adapts to seasonal demands and changing requirements.
Real-time Visibility
Modern systems generate operational data enabling unprecedented visibility, performance monitoring, predictive analytics, and continuous improvement initiatives.
Chapter 4
UK Market Trends and Investment
Market Growth Projections
The UK warehouse automation market, valued at approximately £2.1 billion in 2024, is projected to exceed £3.4 billion by 2030, representing a 19.5% CAGR. Mobile robotics leads growth at over 25% CAGR, followed by AI-powered solutions at 22%.
Investment Focus Areas
- Mobile Robotics (35% of spending): AMRs provide flexibility and scalability
- AI and Machine Learning (40% annual growth): Demand forecasting, optimization, and predictive maintenance
- IoT Infrastructure (30% annual growth): Real-time monitoring and data-driven optimization
- Cloud Software (60% of new implementations): SaaS solutions with rapid deployment
Post-Brexit Market Evolution (2021-2025)
Labour Landscape Changes
- Wage increases of 15-20% since 2021, improving automation ROI
- Accelerated automation timelines by 12-18 months
- Workforce upskilling to work alongside automated systems
Adaptation Strategies
- Hybrid automation models combining selective automation with human workers
- Regional consolidation into fewer, highly automated facilities
- Increased 3PL-vendor partnerships to share costs and expertise
Regulatory and Logistics Impact
- Simplified approval processes accelerate implementation
- Brexit-driven inventory buffer requirements are increasing the need for high-density storage investment
- Enhanced customs compliance, driving documentation automation
Chapter 5
Challenges and Considerations for UK Businesses
High Initial Investment
Comprehensive automation requires investments of £500,000 to £ 10 million or more. Hidden costs include infrastructure modifications, integration expenses, training, and project management. Traditional financing may not align with the depreciation rates and ROI timelines of automation.
System Integration Complexity
Legacy system compatibility challenges include data format incompatibilities, communication protocol mismatches, and performance limitations. Multi-vendor coordination requires interface standardization and extensive testing protocols.
Maintenance and Reliability
Automated systems require disciplined preventive maintenance, spare parts management, and specialized skills. Predictive maintenance, utilizing sensors and analytics, can significantly enhance reliability, while comprehensive disaster recovery planning ensures business continuity.
Skills Gap and Expertise Shortage
Specialized automation skills are in short supply, creating recruitment challenges and requiring significant training investments. Competition for talent drives premium salaries that may strain budgets.
Cybersecurity Risks
Connected systems create vulnerabilities requiring network segmentation, access controls, encryption, and ongoing patch management. Compliance with GDPR and industry standards adds complexity to security implementations.
Chapter 6
Implementing Warehouse Automation Successfully
Planning and Assessment
Success begins with clear, measurable objectives that are aligned with the business strategy. Comprehensive current state analysis includes process mapping, performance baselines, cost analysis, and system inventory. Define operational requirements, including volume patterns, accuracy standards, speed requirements, and flexibility needs.
Technology and Vendor Selection
Utilize systematic evaluation frameworks that map requirements to capabilities, assessing the total cost of ownership, scalability, and integration complexity. Vendor evaluation should consider technology maturity, implementation experience, financial stability, and support capabilities. Proof-of-concept development validates performance before full commitment.
Implementation Management
Effective project governance encompasses the formation of an appropriate team, effective stakeholder engagement, and effective risk management. Phased implementation reduces risk and enables learning, while comprehensive testing protocols ensure reliable operation before deployment.
Training and Change Management
Develop comprehensive training programs for operators, maintenance staff, and management. Effective change management includes clear communication, staff involvement, ongoing support, and recognition programs to encourage adoption.
ROI Measurement and Optimization
Establish KPIs aligned with objectives, implement real-time monitoring, and maintain historical data for trend analysis and informed decision-making. Calculate financial, operational, and strategic return on investment (ROI) while considering relevant risk factors. Continuous improvement processes ensure ongoing optimization and the realization of maximum value.
Chapter 7
Automation Solutions for SMEs and Smaller Warehouses
Unique SME Challenges
SMEs typically work with budgets of £50,000-£500,000, face space constraints in older buildings, require flexible, multi-purpose solutions, and handle lower volumes with greater product variety.
Cost-Effective Entry Points
Modular Systems: Conveyor systems, pick-to-light, cloud WMS, and RFID can be implemented incrementally.
Collaborative Robots: £30,000-£80,000 cobots provide faster implementation with minimal infrastructure requirements and simplified programming.
Cloud-Based WMS: Subscription models make enterprise software accessible with rapid implementation, automatic updates, and scalable licensing.
Semi-Automation: Voice-directed picking, barcode scanning, and automated documentation provide immediate benefits while building capabilities.
Financing Options
- Equipment Leasing: Reduces upfront capital with flexible terms and maintenance inclusion
- Government Grants: Innovation grants, regional development funds, and skills development support
- Vendor Financing: Direct supplier financing and performance-based contracts
- SME-Specific ROI: Focus on operational metrics, time-to-value, and qualitative benefits
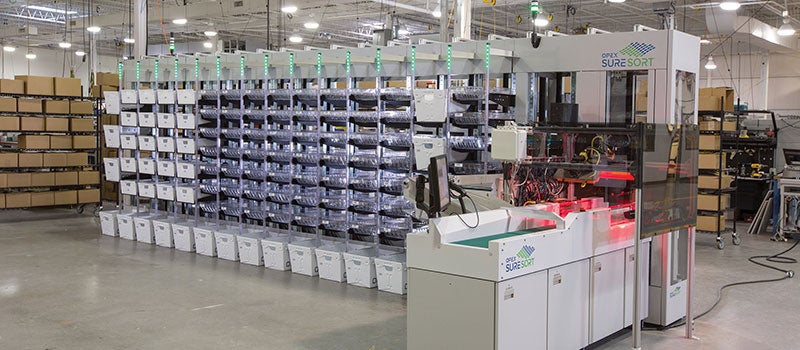
Case Study
Boux Avenue - UK Lingerie Retailer Reduces Temporary Labour by 33%
Boux Avenue, the lingerie and swimwear brand owned by TPRG (Theo Paphitis Retail Group), operates a 23,000 square foot distribution centre serving 30 UK stores and international e-commerce customers with 30,000 SKUs.
- Challenge: Required hiring 250 additional temporary staff during peak seasons, increasing error risk and operational costs due to rising UK inflation and labour shortages
- Solution: Implemented OPEX Sure Sort automated sorting system, transitioning from individual order picking to batch-picking
- Investment: Moderate automation investment with a 4-6 week implementation timeline
- Results:
- 5x increase in orders picked per employee per hour (from 12 to 50 orders)
- 2km reduction in walking distance per work assignment
- 33% reduction in seasonal labour requirements (150 fewer temporary staff)
- System processes over 10,000 orders per day at 1,200 items per hour
- Handles 95% of all products, excluding larger items
- Key Success Factors: Smooth implementation process, rapid system ramp-up, and seamless integration with existing operations
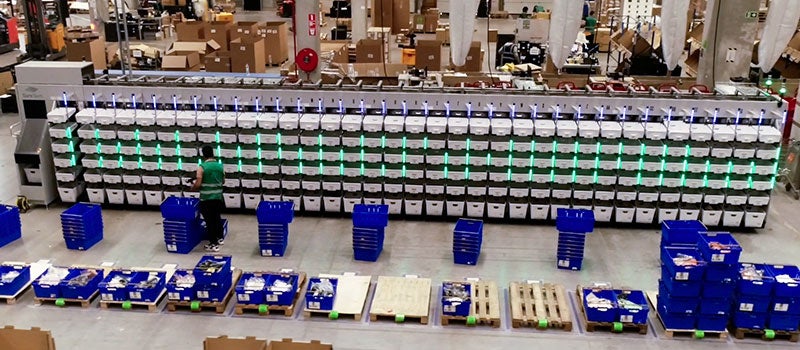
Case Study
Bleckmann - European 3PL Achieves 2x Efficiency Increase
Bleckmann, founded in 1862, is a leading European 3PL specializing in fashion and lifestyle brands with a 120,000 square meter facility in Grobbendonk, Belgium.
- Challenge: Difficulty scanning barcodes and RFID tags hidden in poly-bag packaging, rising labour costs, and need to manage seasonal peaks efficiently
- Solution: First European 3PL to implement OPEX Sure Sort with groundbreaking RFID scan tunnel technology
- Results:
- 2x increase in operational efficiency
- 99% read rate for items (compared to much lower rates with previous barcode scanning)
- 1.3 million items successfully sorted through the system
- Over 32km distance traveled by automated iBots for sorting operations
- Key Success Factors: Innovative technology partnership with OPEX, successful RFID implementation, and focus on addressing specific operational challenges
Chapter 8
Emerging Technologies Reshaping Warehouse Automation
Artificial Intelligence Applications
Demand Forecasting: AI analyses multiple variables, improving forecast accuracy by 15-25% compared to traditional methods.
Predictive Maintenance: Machine learning predicts equipment failures weeks in advance, resulting in a 10-20% reduction in maintenance costs.
Computer Vision: Automated quality control, damage detection, and inventory auditing with greater consistency than human inspection.
Dynamic Slotting: Real-time optimization of storage locations based on demand patterns and operational efficiency.
Advanced AMR Capabilities
Next-generation AMRs incorporate capabilities for picking, sorting, and inventory management. Swarm robotics enables coordinated operations with distributed decision-making and self-organizing behavior. Vision-guided navigation operates in unstructured environments with dynamic obstacle avoidance.
Digital Twins and Simulation
Virtual commissioning validates systems before physical implementation, reducing risk and optimizing design. Real-time digital twins enable continuous optimization through what-if analysis and predictive analytics, allowing for informed decision-making. Virtual training environments offer a safe and cost-effective means of staff development.
Edge Computing and IoT
Edge computing enables real-time decision-making, autonomous operation, and bandwidth optimization. Enhanced sensor networks provide comprehensive environmental monitoring, while wearable technology augments workforce capabilities through AR guidance and health monitoring.
AR and VR Applications
AR-assisted picking provides visual guidance, improving speed and accuracy. Maintenance support through AR enables remote expert assistance and advice on procedures. VR training environments provide realistic simulation and hazard training without exposing individuals to actual risk.
Conclusion
The Strategic Imperative
Warehouse automation has evolved from an optional enhancement to a strategic necessity. The convergence of labour shortages, e-commerce growth, and technology maturation creates unprecedented opportunities for operational improvement and competitive advantage.
Technology Readiness
The market has reached a level of maturity that reduces implementation risk while maximizing benefits. AMRs, AI applications, and cloud software have evolved from experimental to proven solutions with established supplier ecosystems.
Implementation Success Factors
Critical success factors include comprehensive planning, selecting appropriate technology, effective change management, and high-quality vendor partnerships. Organizations investing adequate time in planning consistently achieve better outcomes.
The SME Opportunity
Automation accessibility for SMEs has significantly improved through modular solutions, collaborative robotics, cloud-based software, and alternative financing options. Success stories demonstrate significant operational improvements through targeted investments.
Future-Proofing Strategies
Sustainable automation strategies require open architecture systems, scalable solutions, and continuous learning processes. Organizations must view automation as an ongoing journey rather than a one-time project.
Recommendations for Action
IMMEDIATE
(Next 3 Months):
SHORT-TERM
(3-12 Months):
LONG-TERM
(1-3 Years):
Conduct operation assessments, establish objectives, evaluate technologies, and investigate financing options.
Implement pilot projects, develop implementation plans, begin training programs, and finalize vendor relationships.
Execute phased implementation, expand capabilities, develop internal expertise, and plan next-generation adoption.
The Competitive Reality
Organizations delaying automation risk falling behind competitors, already realizing operational benefits. The advantages of automation compound over time, making it increasingly difficult for manual operations to compete effectively.
The UK warehouse automation market offers unprecedented opportunities for organizations of all sizes. The technologies are proven, the vendor ecosystem is mature, and financial models are accessible. Success requires strategic thinking, careful planning, and decisive action to capture competitive advantages for long-term success.
Warehouse automation represents the transformation of UK warehousing through the augmentation of human capabilities, improved working conditions, and more efficient, safe, and profitable operations. Organizations embracing this perspective will lead the next generation of UK warehouse operations.
Other Resources You Might Find Helpful
NEXT LEVEL AUTOMATION
Unlock Operational Efficiency with OPEX
OPEX is powering the future of automation. Contact us to learn more about how our vertically integrated automated solutions can help take your business to new heights.