Which Automation Technologies are Right for Your Warehouse? An Overview of AGVs, AMRs, and More
4 min read
60-Second Summary
Warehouse automation is rapidly becoming essential for UK logistics operations striving for greater efficiency and resilience. This blog breaks down key technologies, from AGVs and AMRs to AS/RS, conveyors, robotics, and sort-to-order systems, explaining how each supports specific challenges like space constraints, labour shortages, and complex order profiles. By understanding how these solutions work and where they fit best, UK warehouse professionals can make informed decisions that improve productivity, scalability, and Return on Investment (ROI), ensuring long-term competitiveness in a fast-evolving market.
Why UK Warehouses Are Turning to Automation – And How to Choose the Right Solution
The drive for greater efficiency and resilience in UK logistics has put warehouse automation firmly in the spotlight. However, the world of automation can seem daunting, filled with acronyms and advanced machinery. For many warehouse and logistics professionals, the critical question isn’t whether to automate, but which technologies are the most suitable for their unique operations.
Understanding the core functions and applications of various automation technologies is the first step towards a more efficient and profitable warehouse. This overview will demystify some of the most impactful solutions, from mobile robots to sophisticated sorting systems, all while keeping the distinct needs of the UK market in mind.
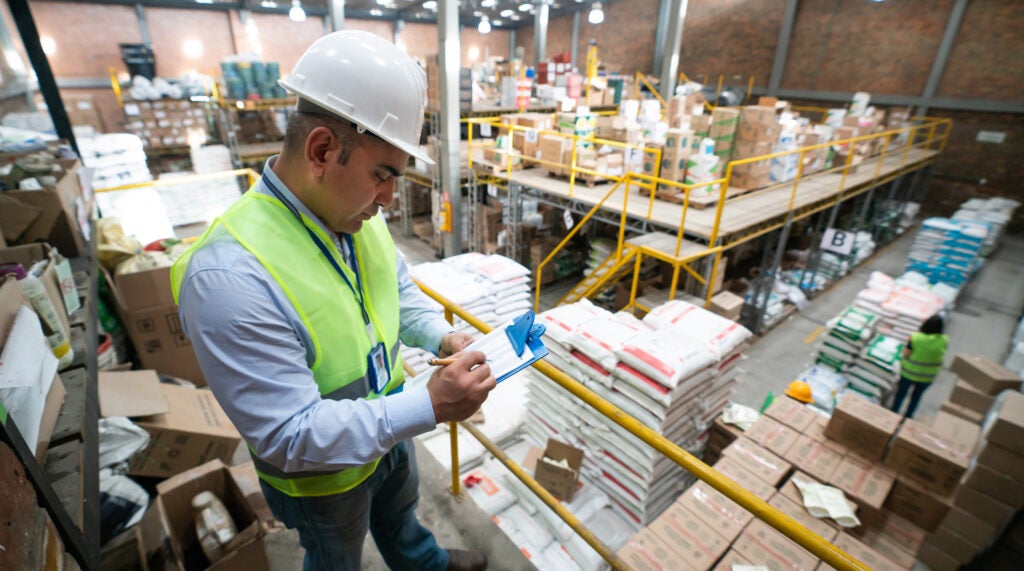
Navigating the Automation Landscape: Key Technologies Explained
While the array of automation solutions is broad, several key technologies form the backbone of modern automated warehouses. Each offers distinct advantages and is designed to tackle specific operational challenges.
Automated Guided Vehicles (AGV’s): The Workhorse of Repetitive Transport
AGVs have been a staple in automated warehouses for decades. These robust, driverless vehicles follow fixed paths, typically guided by wires embedded in the floor, magnetic tape, or lasers that detect reflectors
How they work: AGVs operate on predefined routes, making them ideal for repetitive, point-to-point transportation of heavy loads. They are programmed to pick up and drop off materials at specific locations, ensuring consistent and predictable movement.
Key applications: Common uses in UK warehouses include transporting pallets between receiving and storage, moving goods from production lines to outbound staging areas, and linking different zones within a large facility. Their reliability and capacity for heavy lifting make them valuable for structured environments.
Pros for UK businesses: AGVs excel in predictable environments, offering high throughput for routine transport tasks. They contribute to a safer workplace by reducing manual handling of heavy goods and can operate continuously.
Automated Mobile Robots (AMRS): The Agile Navigators of the Warehouse Floor
AMRs represent a significant evolution from AGVs. Unlike AGVs, AMRs navigate dynamically using onboard sensors, cameras, and sophisticated software to understand their environment, detect obstacles, and plot the most efficient routes in real-time.
How they work: AMRs don't require fixed pathways. They use simultaneous localization and mapping (SLAM) technology to build a map of their surroundings and navigate around people, equipment, and other robots. If an obstacle appears, an AMR will find an alternative route, ensuring continuous operation.
Key applications: AMRs are highly versatile. They are increasingly popular in UK e-commerce fulfilment centres for goods-to-person picking, where robots bring shelves or inventory directly to human pickers. They can also be used for order sortation, inventory counting, and even cleaning.
Pros for UK businesses: Their flexibility makes them ideal for dynamic environments where layouts might change or where human interaction is frequent. AMRs enhance productivity by reducing picker travel time and can be quickly scaled up or down based on demand, offering agility in volatile markets. Their ease of integration with existing infrastructure is also a significant advantage.
Automated Storage and Retrieval Systems (AS/RS): Maximising Space and Speed
AS/RS are sophisticated systems designed for high-density storage and rapid, automated retrieval of inventory. They come in various forms, including unit-load (for pallets) and mini-load (for cases or totes), as well as shuttle-based systems.
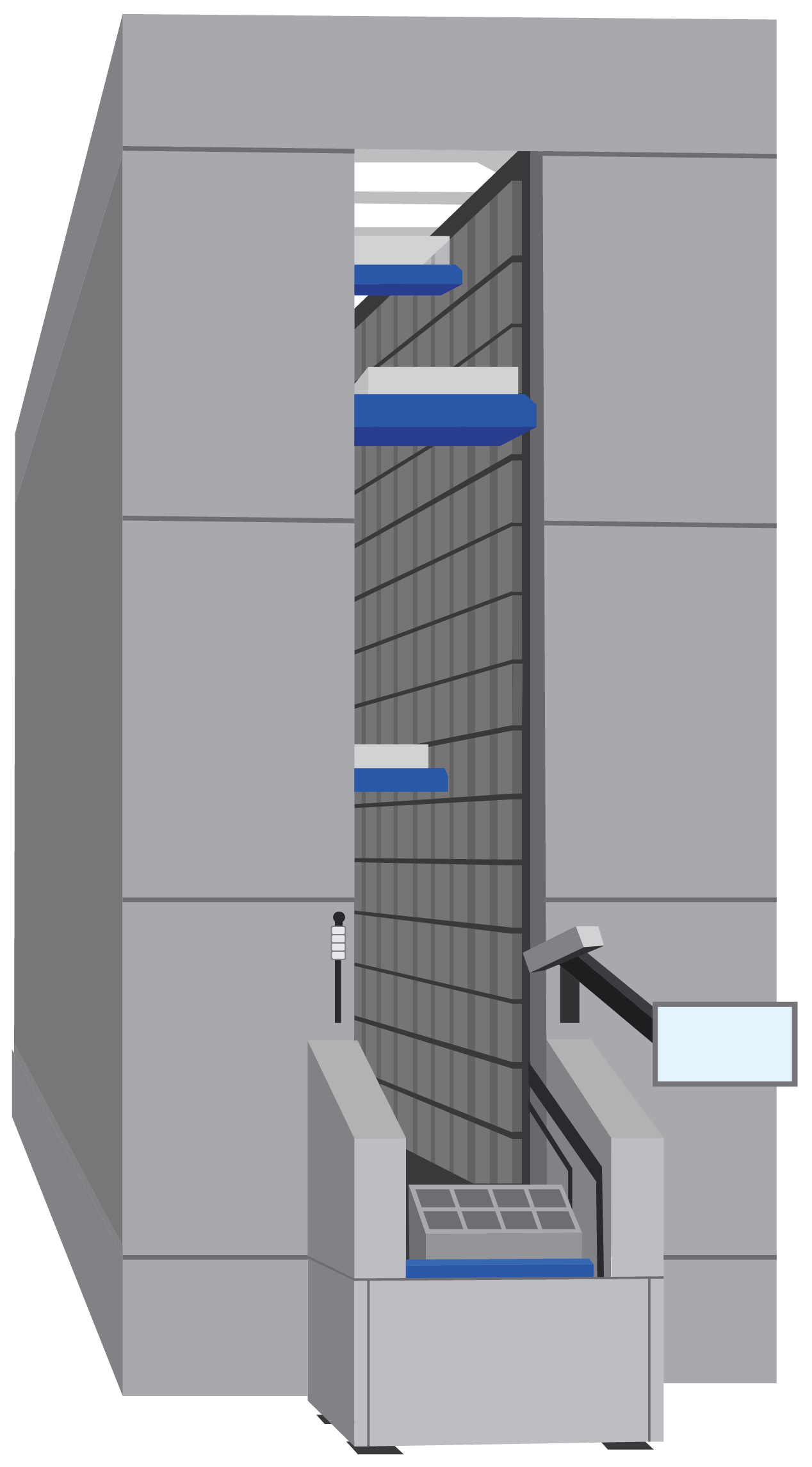
How they work: AAS/RS typically consists of racks, storage and retrieval (S/R) machines, and a control system. The S/R machines travel vertically and horizontally to store and retrieve items from designated locations within the high-density racking structure. Shuttle systems use small, fast robots that move independently on levels within the racking.
Key applications: These systems are ideal for warehouses that handle high volumes of stock-keeping units (SKUs), have limited floor space, or require rapid access to inventory. Many large distribution centres and e-commerce operations in the UK leverage AS/RS to maximise storage density and accelerate order fulfilment.
Pros for UK businesses: TAS/RS dramatically reduces the physical footprint required for storage, a crucial benefit given the premium on industrial property in the UK. They offer exceptional throughput, improve inventory accuracy, and enhance security for valuable goods.
Conveyors: The Lifelines of Material Flow
Conveyor systems are arguably the most common form of automation in warehouses. They are essential for transporting goods, cases, and totes between different workstations, zones, or stages of the fulfilment process.
How they work: Conveyors use motorised belts, rollers, or chains to move items along a predefined path. They can be gravity-fed, powered, or accumulate goods to manage flow.
Key applications: Conveyors are integrated into almost every automated warehouse design, moving products from receiving to sortation, through picking zones, and to packing and shipping. They are vital for creating a continuous flow of goods and minimising manual handling.
Pros for UK businesses: Conveyors provide a cost-effective method for efficiently moving high volumes of items. They reduce manual effort, improve safety, and can be configured to create highly optimised workflows for specific processes.
Robotics: Precision and Versatility in Action
Beyond AGVs and AMRs, industrial robots are increasingly being deployed for a variety of tasks that require precision, speed, and repetitive motion. These can include robotic arms, collaborative robots (cobots), and specialised grippers.
How they work: Robotic arms are stationary or mounted on rails and perform tasks such as picking individual items (piece picking), packing, palletising, or depalletising. Cobots are designed to work safely alongside humans, allowing for collaborative workflows.
Key applications: Robotic piece picking is gaining traction for e-commerce, where varied product sizes and shapes pose a challenge. Robotics are also used for high-speed sortation, loading/unloading containers, and intricate assembly tasks.
Pros for UK businesses: Robots offer unparalleled precision and consistency, reducing errors and product damage. They can perform repetitive, ergonomically challenging tasks, freeing human workers for more complex roles, and contribute to significant labour efficiency.
Automated Sort-To-Order Systems: Precision at Scale
As order profiles become more complex, especially with the rise of direct-to-consumer (D2C) and omnichannel fulfilment, efficient sortation is critical. Automated sort-to-order systems ensure that individual items or totes are routed to the correct packing station or shipping lane for consolidation into customer orders.
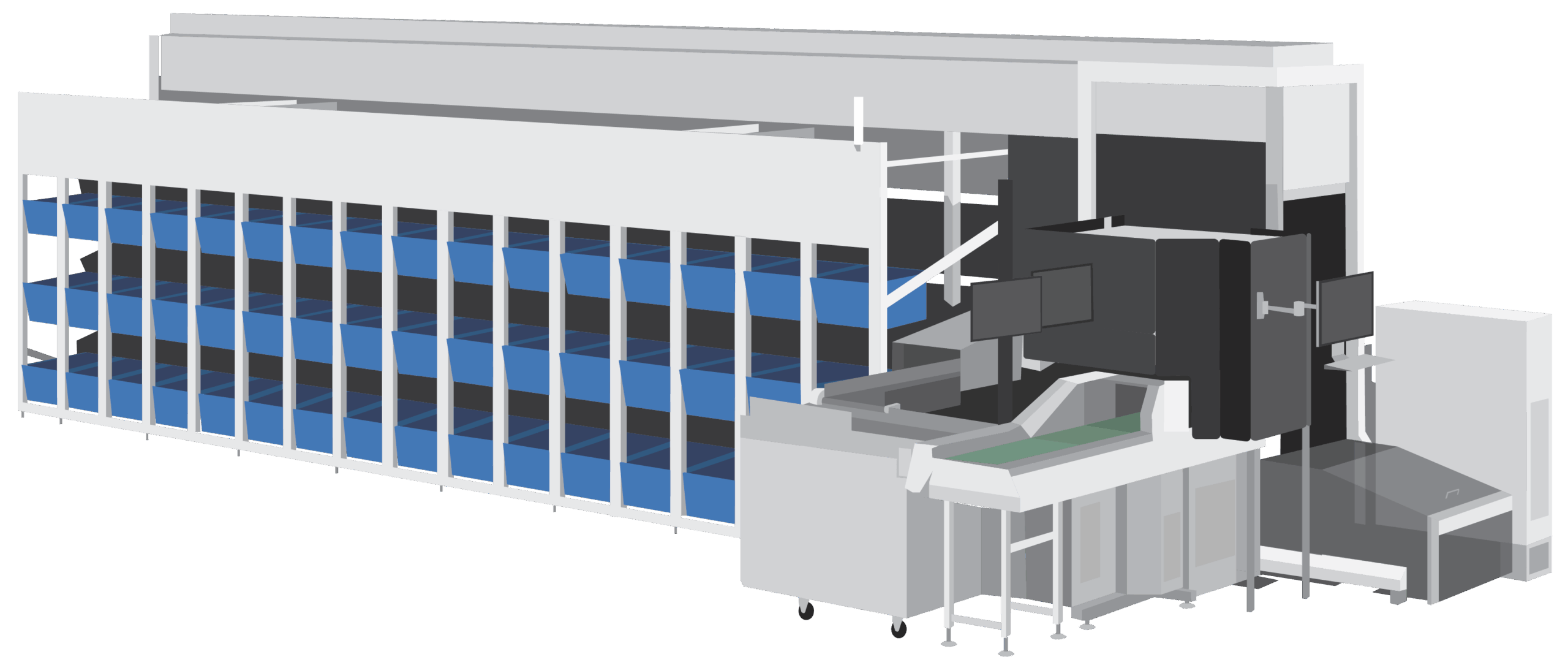
How they work: These systems utilise high-speed conveyors, diverters, and sometimes robotic arms or tilt-tray sorters to direct items based on their unique identification (e.g., barcode scan) to the correct order accumulation zone. They often work in conjunction with WMS/WCS to manage the flow and ensure accurate sorting.
Key applications: Essential for e-commerce, retail fulfilment, and parcel delivery hubs where large volumes of individual items need to be sorted into specific customer orders or delivery routes. Many UK fulfilment centres rely on these systems to meet stringent delivery deadlines.
Pros for UK businesses: Automated sort-to-order systems dramatically increase sorting speed and accuracy, reducing manual intervention and errors. This directly translates to faster order fulfilment, lower shipping costs, and improved customer satisfaction, which are vital for competitive advantage in the UK market.
Choosing the Right Fit: A Strategic Decision for UK Operations
The “right” automation technology is not a one-size-fits-all solution. It’s a strategic decision that depends on a thorough understanding of your warehouse’s specific challenges, goals, and operational characteristics.
Analyse Your Throughput Needs:
Do you need to process thousands of orders per hour, or are your volumes more moderate? High throughput often points towards AS/RS, high-speed conveyors, and automated sort-to-order systems.
Consider Your Product Mix:
Are you handling pallets, cases, or individual items? The size, weight, and fragility of your products will dictate suitable handling technologies.
Evaluate Your Labour Availability and Costs:
Are you struggling to find enough staff? Automation can alleviate labour pressures and allow you to redeploy valuable human resources.
Assess Your Space Constraints:
Is your warehouse running out of room? AS/RS and dense storage solutions can maximise your existing footprint.
Define Your Desired ROI:
What are your financial goals for automation? Cost savings, efficiency gains, and improved customer satisfaction all contribute to ROI.
Future Scalability:
Will your automation system need to grow with your business? AMRs and modular conveyor systems offer greater flexibility for future expansion.
Understanding these critical factors will guide you toward the technologies that offer the greatest impact and return for your specific UK warehouse operation.
The Path to an Automated Future
The UK logistics sector is at a pivotal moment. Embracing warehouse automation is no longer a luxury but a necessity for businesses aiming to remain competitive, resilient, and profitable. By familiarising yourself with the core technologies—from the reliable AGVs to the agile AMRs, space-saving AS/RS, essential conveyors, versatile robotics, and precision sort-to-order systems—you can begin to chart a course for a more efficient and future-proof warehouse.
Ready to explore these technologies in detail and understand how to integrate them into your UK warehouse?
Read our in-depth guide, “The Definitive Guide to Warehouse Automation in the UK” for in-depth information on each technology, a comprehensive breakdown of their benefits, and practical guidance on how to choose the best fit for your specific operational needs.
Other Resources You Might Find Helpful
NEXT LEVEL AUTOMATION
Unlock Operational Efficiency with OPEX
OPEX is powering the future of automation. Contact us to learn more about how our vertically integrated automated solutions can help take your business to new heights.