Optimising Operations: Strategies for Efficiency and Cost Control in UK Logistics
15 min read
60-Second Summary
UK logistics and warehouse operators are under pressure to deliver more quicklyfaster, more cost-effectively, and accurately amid labour shortages, rising costs, and post-Brexit challenges. This guide explores how integrating warehouse software, automation, smarter layouts, and collaborative logistics can significantly boost efficiency and cost control. By embracing technologies like WMS, AS/RS, and predictive analytics, and while improving forecasting and layout strategies, businesses can streamline operations, cut waste, and enhance resilience—, ultimately positioning themselves for scalable, sustainable growth.
Optimising Operations: Strategies for Efficiency and Cost Control in UK Logistics
UK warehouse and logistics operators face mounting pressure to deliver faster, cheaper, and more accurately without compromising quality or compliance. From labour shortages and rising energy costs to post-Brexit supply chain friction and customer expectations for same-day delivery, achieving operational excellence is more critical than ever.
This guide examines practical, technology-driven strategies to enhance warehouse performance, optimise costs, and establish a more resilient and responsive operation.
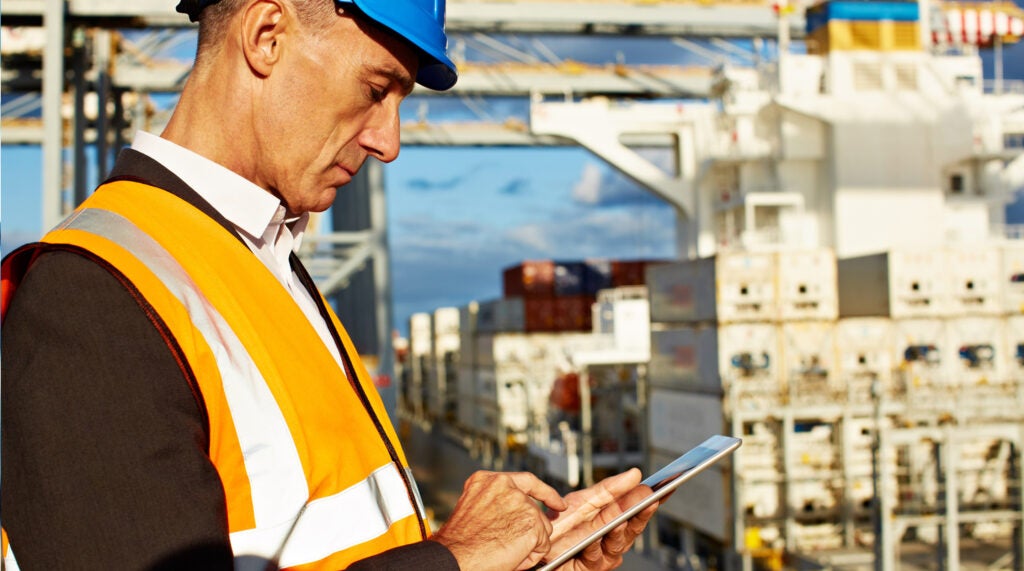
The Case for Efficiency an Cost Control
Operational inefficiencies cost UK logistics firms millions each year. These often stem from manual processes, fragmented systems, poor warehouse layout, or siloed data. The result? Lost productivity, avoidable errors, higher fulfilment costs, and ultimately, dissatisfied customers.
Improving efficiency isn’t just about speed, it’s about eliminating waste, maximising resources, and creating a seamless flow from goods-in to delivery. Efficiency directly influences profitability and customer retention, making it a top strategic priority for warehouse leaders.

Technology as the Backbone of Smarter Warehousing
WMS, WES and WCS Integration
Warehouse Management management Systems systems (WMS), Execution execution Systems systems (WES), and Control control Systems systems (WCS) are the digital backbone of a modern operation. Integrated platforms can:
- Offer real-time visibility of inventory and workflows.
- Automate routine tasks, such as routing and wave picking.
- Synchronise automated equipment like AS/RS or robotic sorters.
- Enable predictive analytics and better demand forecasting.
These systems drive speed and reduce errors, overtime, and manual labour reliance. Cloud-based WMS solutions are becoming increasingly appealing to small and medium-sized enterprises (SMEs) seeking scalability with lower upfront investment.
Automation for Consistency and Accuracy
Automation doesn’t just replace manual labour— it standardises processes, improves safety, and unlocks scalable growth.
Solutions such as these include:
- Automated sorting systems (e.g., Sure Sort® X) can process up to 2,100 items per hour with minimal human intervention, significantly improving throughput and reducing error rates.
- Goods-to-person AS/RS ,like Perfect Pick®, help maximise vertical space and minimise walking time, delivering totes directly to pickers for ergonomic and accurate fulfilment.
Even semi-automated enhancements, such as voice-picking or mobile handheld scanners, can yield immediate productivity gains for operations not ready for full automation.
Process Improvement: Layout, Flow, and Space
Warehouse design plays a central role in operational performance. Poor layout leads to congestion, long travel paths, and inefficient pick rates. Consider:
- Slotting optimisation to prioritise high-frequency SKUs in easy-access locations.
- Batch, wave, or zone picking strategies based on order profiles.
- Return flow planning to integrate reverse logistics with minimal disruption.
Evaluating workflows from receiving through to dispatch— and reconfiguring layouts with simulation software— can reveal significant gains with minimal investment.
Better Forecasting and Cross-Team Coordination
Forecasting accuracy and interdepartmental communication are major stumbling blocks. When warehouse, procurement, and sales teams work in silos, bottlenecks emerge.
Effective Sales & Operations Planning (S&OP), underpinned by shared data platforms, allows for:
- Smoother alignment between inventory levels and order volume.
- Pre-emptive resource planning during seasonal peaks.
- Improved supplier collaboration and inbound coordination.
When combined with predictive analytics, businesses can react to demand variability without overstocking or missing service-level agreements (SLAs).

The Power of Collaborative Logistics
Cost control isn’t only internal. Collaborating with external partners, including suppliers, 3PLs, and even competitors, can reduce duplication and unlock shared efficiencies:
- Vendor Managed Inventory (VMI) reduces stockouts and carrying costs.
- Shared transport models reduce empty mileage and carbon emissions.
- Integrated platforms with suppliers or retailers improve order accuracy and reduce lead times.
These models are increasingly supported by APIs and cloud-based systems that allow seamless data exchange without complex custom integrations.

Addressing Peak Demand, Security and Sustainability
Seasonal Peaks:
Automated systems like Sure Sort X with Xtract™ allow rapid scalability during peak periods, handling up to 1,800 units and 200 orders per hour while reducing the need for seasonal staff.
Security and Shrinkage:
Real-time tracking through WMS and automation can also reduce shrinkage, mispicks, and theft. Systems like Perfect Pick enable secure item storage and traceability, limiting access to only authorised personnel.
Green Warehousing:
Energy-efficient solutions, like low-power sorters or solar-powered facilities, help reduce long-term operational costs. Efficient automation supports sustainability targets by reducing energy consumption per processed order.
Future-Proofing Through Smarter Operations
Operational excellence in UK logistics is no longer a choice, it’s a competitive imperative. When strategically deployed, technology enables teams to accomplish more with less, adapt more quickly, and serve customers more effectively.
By focusing on key levers such as software, automation, layout, planning, and collaboration, businesses can take control of their operational destiny, reducing costs while enhancing service, resilience, and growth potential.
Contact us today for a meeting or demo of our products.
Other Resources You Might Find Helpful
NEXT LEVEL AUTOMATION
Unlock Operational Efficiency with OPEX
OPEX is powering the future of automation. Contact us to learn more about how our vertically integrated automated solutions can help take your business to new heights.