Boosting The Bottom Line: Practical Approaches to Cost Control in Warehousing
4 min read
60-Second Summary
UK warehousing is entering a new era, where emerging technologies like AI, digital twins, edge computing, and AR/VR are reshaping how warehouses operate. These innovations go beyond traditional automation, enabling smarter forecasting, real-time optimisation, precision sorting, and immersive training. Once reserved for tech giants, these tools are now increasingly accessible to businesses of all sizes. Early adoption and strategic planning can help UK logistics firms future-proof operations, improve efficiency, and stay competitive in an evolving landscape driven by intelligence and agility.
Embracing The Future: How Emerging Technologies Are Redefining UK Warehousing
The UK’s logistics and warehousing sector is in a state of continuous evolution. While traditional automation solutions, such as AS/RS and standard conveyors, remain foundational, a new wave of cutting-edge technologies is rapidly transitioning from the experimental phase to practical application. For forward-thinking businesses in the UK, understanding these emerging innovations is crucial for future-proofing operations and maintaining a competitive edge.
These advanced technologies leverage data, artificial intelligence, and enhanced connectivity to create smarter, more agile, and more resilient warehouses. They are not merely incremental improvements but represent a fundamental shift in how materials are handled, decisions are made, and workflows are optimised.
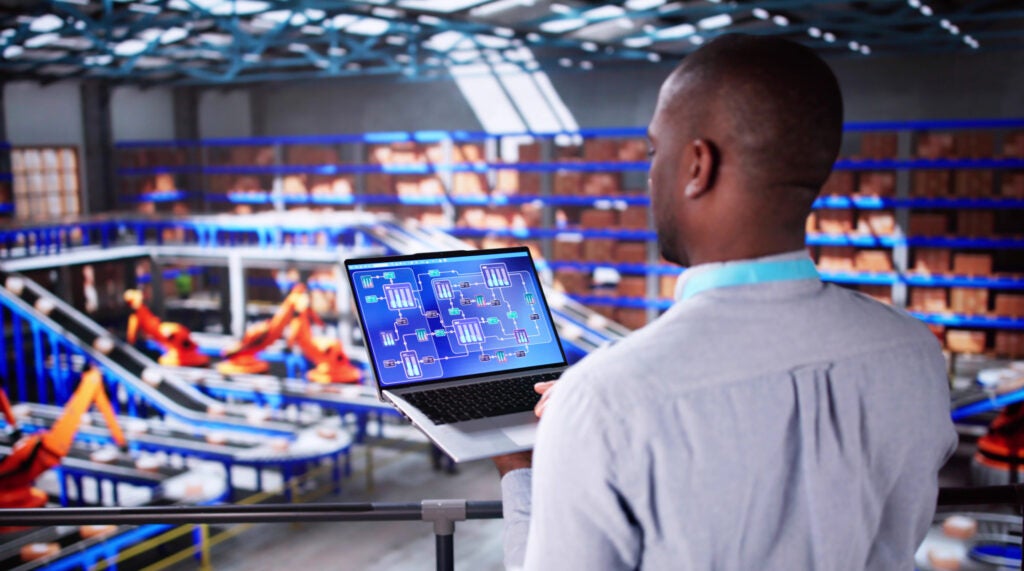
The Next Frontier: Innovations Reshaping UK Warehousing
Here’s a look at some of the key emerging technologies that are poised to transform UK warehouses:
Artificial Intelligence (AI) For Advanced Demand Forecasting and Optimisation
How It works:
including historical sales, seasonality, promotions, weather patterns, and even social media sentiment – to generate highly accurate demand forecasts. In the warehouse, AI optimises slotting, picking paths, and resource allocation in real-time.
Applications in UK Warehouses:
- Predictive Inventory Management: AI helps prevent overstocking and stockouts, reducing carrying costs and improving service levels. For example, AI can predict shipment lead times and identify potential equipment anomalies before breakdowns occur.
- Optimised Picking and Putaway: AI algorithms can dynamically adjust product placement based on demand patterns, recommending that high-demand items be placed closer to shipping areas to reduce picking times.
- Real-time Decision Making: AI can identify at-risk orders, spot mistakes like mislabelled packages using computer vision, and even help train and control robots.
Impact in the UK:
Over half of UK fulfilment centres are projected to use AI in their operations by 2025, rising to 70% by 2027. By the end of the decade, AI is anticipated to handle over 90% of warehouse logistics tasks globally, setting a new industry standard.
Automated Sort-To-Order Systems: Precision and Speed for UK Fulfilment
How it works:
Traditional manual sortation is a labour-intensive bottleneck, particularly with the explosion of e-commerce and the need for accurate, individual order consolidation. Automated sort-to-order systems, like OPEX’s Sure Sort® X with Xtract™, utilise advanced technology to direct individual items to their specific customer orders rapidly. These systems employ high-speed conveyors and intelligent robotic diverters or chutes to sort items based on barcode scans or other unique identifiers. Items flow through the system, are identified, and are then automatically directed to the correct packing chute or order bin, ready for consolidation and dispatch.
Applications in UK Warehouses:
High-Volume E-commerce Fulfilment: For UK online retailers and 3PLs handling thousands of daily orders, these systems ensure that each item is quickly and accurately routed to its corresponding order, even for multi-line orders with diverse SKUs. This significantly reduces manual handling and picking errors, which are critical for meeting demanding customer delivery expectations.
- Batch Picking Optimisation: Instead of pickers travelling to individual items for each order, they can pick multiple orders in a batch. The automated sort-to-order system then takes these batch-picked items and precisely sorts them into individual customer orders, dramatically increasing picking efficiency.
- Returns Processing: These systems can also be configured to efficiently sort returned items, directing them to appropriate locations for restocking, quality control, or disposal, streamlining a complex and often costly process.
- Order Consolidation and Dispatch: By precisely sorting items into complete customer orders, these systems prepare shipments for efficient packing and dispatch, reducing the need for manual consolidation and speeding up the outbound process.
Impact in the UK:
The escalating demands of e-commerce have made high-speed, accurate sortation an indispensable capability. Reports indicate that over half of UK fulfilment centres are projected to use AI in their operations by 2025, rising to 70% by 2027, with automated sorting being a prime beneficiary of AI-driven optimisation. This technology enables UK businesses to handle unprecedented order volumes, significantly improve order accuracy (often achieving near 100%), and reduce the labour hours associated with manual sorting and consolidation. The ability to rapidly sort thousands of items per hour translates directly to faster customer deliveries and enhanced operational profitability.
Digital Twins For Simulation and Optimisation:
How it works:
A digital twin is a virtual replica of a physical warehouse, process, or system, continuously updated with real-time data from IoT sensors, WMS, and other systems. This living model allows businesses to simulate changes, test new layouts, predict performance, and identify bottlenecks without disrupting physical operations.
Applications in UK Warehouses:
- Layout Optimisation: A UK-based retailer reportedly identified a 17% space utilisation improvement by testing various configurations in their digital twin.
- Scenario Planning: Prepare for peak seasons, integrate new technologies (like AMRs), or simulate responses to supply chain disruptions in a risk-free virtual environment.
- Predictive Maintenance: Monitor equipment health in the digital twin to anticipate failures, reducing downtime by up to 45%.
Impact in the UK:
The global digital twin market is projected to grow by up to 45% annually between 2023 and 2030. The UK government recognises the strategic importance of this technology, with initiatives supporting its development and application across various sectors, including optimising warehouse management processes.
Edge Computing for Real-Time Decision Making:
How it works:
Edge computing processes data at or near the source (e.g., on a sensor, robot, or local server within the warehouse) rather than sending it all to a centralised cloud. This significantly reduces latency, enabling real-time data analysis and immediate decision-making at the operational level.
Applications in UK Warehouses:
- Real-time Robotics Control: Instantaneous communication between robots and central systems for collision avoidance, dynamic path planning, and task execution.
- Enhanced Vision Systems: Processing high-bandwidth video data from cameras locally for real-time quality control, stock counting, and security monitoring without overloading the network. DHL’s collaboration with Protex AI, for example, uses edge devices for computer vision and AI to generate proactive safety events in logistics.
- Predictive Maintenance on Site: Analysing sensor data from equipment locally to predict failures before they occur, allowing for immediate intervention.
Impact in the UK:
As warehouses become more data-intensive, the need for real-time processing grows. Edge computing is crucial for enhancing the responsiveness and efficiency of interconnected warehouse systems, improving data security, and reducing bandwidth usage.
Augmented Reality (AR) and Virtual Reality (VR) for Training and Operations:
How it works:
- AR (Augmented Reality): Overlays digital information onto the real world (e.g., smart glasses displaying picking instructions, product locations, or maintenance overlays for equipment).
- VR (Virtual Reality): Creates fully immersive simulated environments (e.g., for training new employees on complex machinery or navigating a virtual warehouse layout).
Applications in UK Warehouses:
- Picker Efficiency: AR smart glasses can guide pickers directly to the correct location and display picking quantities, reducing errors and improving speed.
- Accelerated Training and Onboarding: VR simulations allow new warehouse operatives to practice tasks, operate equipment, and navigate complex layouts in a risk-free virtual environment, significantly reducing training time and increasing safety. This also helps with consistency of training quality.
- Remote Maintenance and Troubleshooting: AR can provide remote experts with a real-time view of equipment issues, guiding on-site technicians through complex repairs.
Impact in the UK:
VR training has become essential for warehouse operations, offering realistic, hands-on learning experiences that improve efficiency, enhance safety by allowing risk-free practice of high-risk tasks, and often prove more cost-effective in the long run by reducing the need for physical materials and minimising downtime.
The Future is Now: Early Adopters and Strategic Planning
Leading UK logistics players like Amazon and Ocado have long been early adopters of advanced robotics and software, paving the way for wider industry adoption. However, the democratisation of technology, as evidenced by the increasing accessibility of AI and robotics for SMEs, means these cutting-edge solutions are becoming available to a broader range of businesses.
For UK businesses planning their technology roadmap, the integration of these emerging technologies is not a distant dream but a tangible opportunity. Strategic planning involves:
- Assessing Current Needs: Identify the specific bottlenecks, challenges, and areas where emerging technologies can deliver the most significant impact.
- Piloting Solutions: Consider piloting new technologies in a controlled environment to assess their effectiveness and integration with existing systems.
- Investing in Skills: Prepare your workforce for the future by investing in training for new roles in AI logistics analysis, automation engineering, and system supervision.
Embracing these cutting-edge innovations will be critical for UK warehouses to not only meet the escalating demands of modern logistics but also to gain a sustainable competitive advantage. The future of warehousing is intelligent, connected, and continuously optimising.
For a deeper analysis of each emerging technology’s applications, detailed implementation requirements, and expert insights into future developments in the UK logistics landscape, delve into our comprehensive guide. Check out: “Emerging Technologies Reshaping Warehouse Automation” section of “The Definitive Guide to Warehouse Automation in the UK” for deeper analysis of each technology’s applications, implementation requirements, and future development, helping you stay ahead of the curve.
Other Resources You Might Find Helpful
NEXT LEVEL AUTOMATION
Unlock Operational Efficiency with OPEX
OPEX is powering the future of automation. Contact us to learn more about how our vertically integrated automated solutions can help take your business to new heights.